Company:
Taiyo Middle East LLC
Project Details
Fabric 1
SGM-30 PTFE-coated fiberglass mesh (special Tan color)
Producer/Manufacturer:
Saint-Gobain Technical Fabrics
Primary Use:
Main Fabric
Engineer Company 1
Maffeis Engineering
Architect Company
Adrian Smith + Gordon Gill Architecture
Fabrication Company
Shanghai Taiyo Kogyo
Subcontractor Company
Taiyo Middle East LLC
Project Manager Company
Taiyo Middle East LLC
Installation Company
Taiyo Middle East LLC
Please describe the project specifications
The Al Wasl Plaza Dome at the 2020 World Expo in Dubai is the center piece of this grandiose event. The Dome has 130m diameter, a height of 65m, and is composed of 631 panels, divided in 30 unique shapes with unique curved seamlines, all together covering a surface of 17.400 sq.m. The specially developed tan color PTFE-coated fiberglass mesh ensures the perfect interface to make this structure the biggest 3D projection mapping screen on Earth.
From the beginning this ambitious project raised major concerns on all stakeholders in regards to its final visual performance and constructability. Our company has been selected by the client before actual construction tender, solely to develop the fabric design and test it, in all visual aspects, via full scale mockups, so ensuring that the architectural intent would be met flawlessly.
Two key elements of expertise brought by our group were the adequate material selection (in terms of type, typology and color) and how to optimize the membrane frame application on the structure.
On the first one, several kinds of fabric materials, with different colors and properties were presented and tested until reaching the suitable material (PTFE-coated fiberglass mesh) and its color (a special tan grade) so to maximize the visual performance interface with the projection.
In relation to the steel frame, instead of using the initially conceived steel arches, our team presented the client with curved seam lines to follow the visual intent of a fluid flowing from top to bottom. This development, along with the special aluminum frame system attached to the main structure, reflected not only on an economical optimization, but also delivered an extraordinary slim support frame. This also resulted on a feeling of flying fabric panels within each oculus, as well as improved the 3D projection mapping final quality.
Later, our company was also commissioned with the design development, shop drawings, engineering, fabrication and installation of the complete tensioned membrane system.
After the end of this World Expo, the dome will continue to play a central role – literally and metaphorically –as part of the legacy to the local community. The surrounding buildings will be converted into hotels and other commercial uses, complementing the entire mixed-use legacy of the Expo site. The location will further strengthen Dubai’s thriving events scene, being it adaptable to host experiences of all sizes and purposes, whether a small, intimate event or a large gathering of up to 10.000 people (such as National Day celebrations).
What is unique or complex about the project?
The project size, material selection and location fit perfectly our company portfolio of capabilities. Additionally, we envisioned at an early stage that our group expertise in membrane technology could highly benefit the project. This was recognized by the client, who engaged with us already on an early stage.
Differently than the projects we did on the past years, where material selection and connection system were defined, on this project its feasibility depended on the correct expert solution we provided. The selection of the membrane, ending on a selection of PTFE-coated fiberglass mesh fabric of a special custom-made tan color was of paramount significance to create the final desired projection screen effect.
Consequently, the possibility to have a membrane structure going beyond its own shape on the space and becoming a live environment via video mapping - or simply “projection mapping” – increased our engagement to the project. The tight tolerance and perfection on execution requirements were integral parts of our delivery to the client, which was finally responsible to ensure the high quality of the 3D mapping.
The fabrication and Installation of the tan PTFE-coated fiberglass mesh had to go through extremely detailed quality control processes, from the raw material inspection (specially towards color uniformity), to fabrication controls (clean welding and set up on curved seams) at the same time optimizing sustainability (through very low wastages).
Our company’s installation and construction team dealt with several additional challenges, including: the unique height and scale of structure, curved aluminum extrusion frames on curved fabric panels, and above all, that the needed precision in tensioning the fabric panels had to be exactly enough to guarantee the functionality, esthetical appearance and durability required. This led us to develop special methods of construction, taking into consideration all these challenges and applying them until the last fabric panel was in place.
Content is submitted by the participant. IFAI is not responsible for the content descriptions of the IAA award winners.
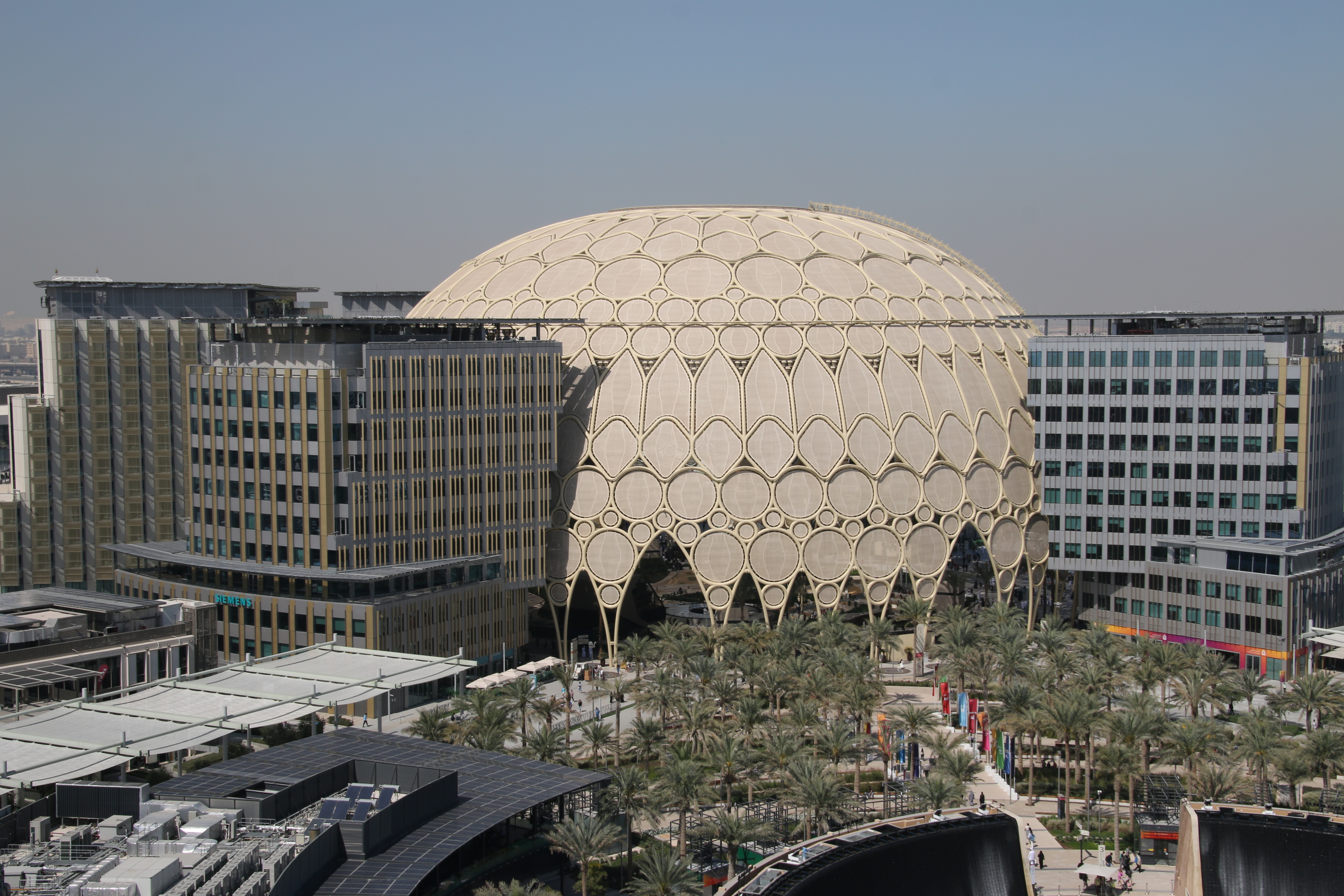
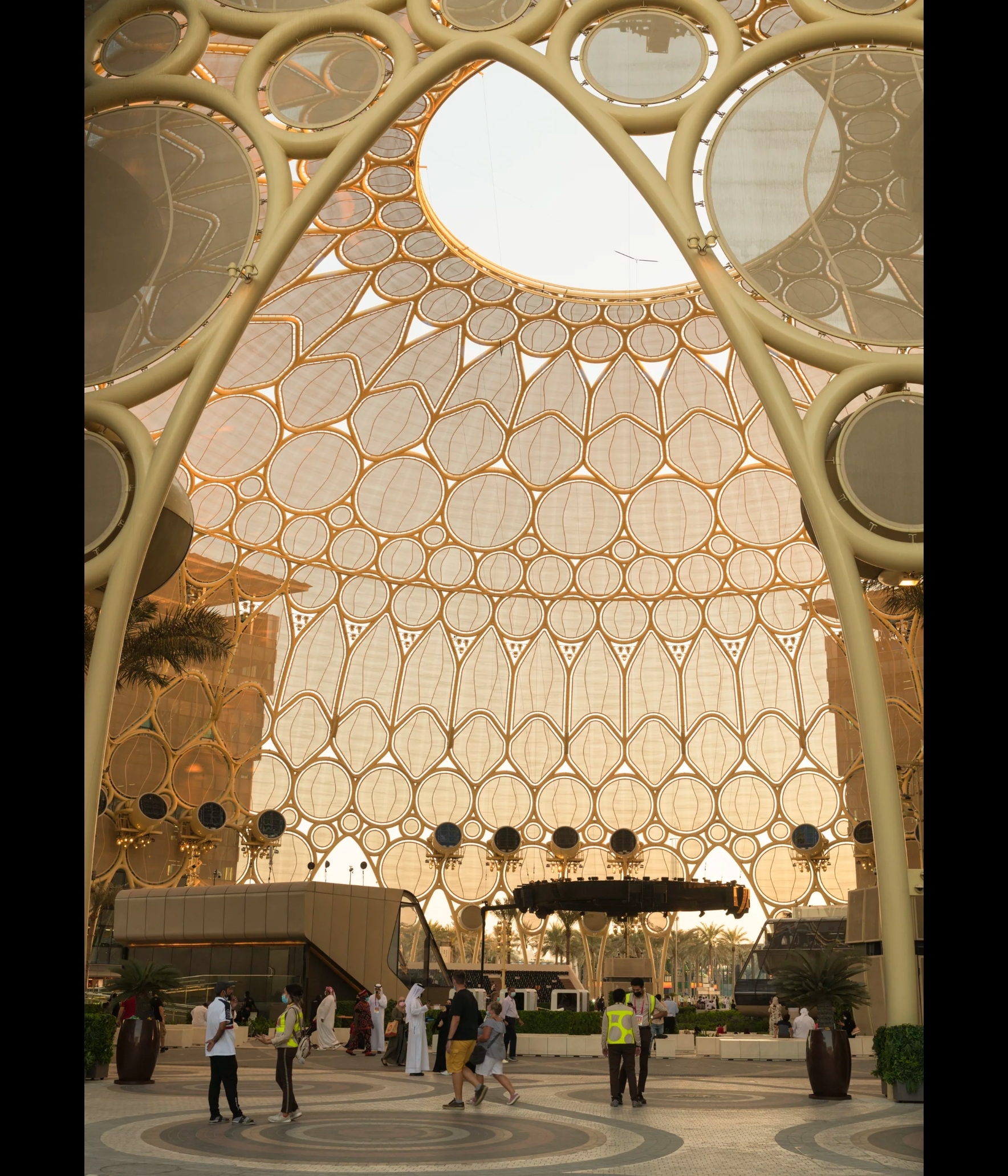
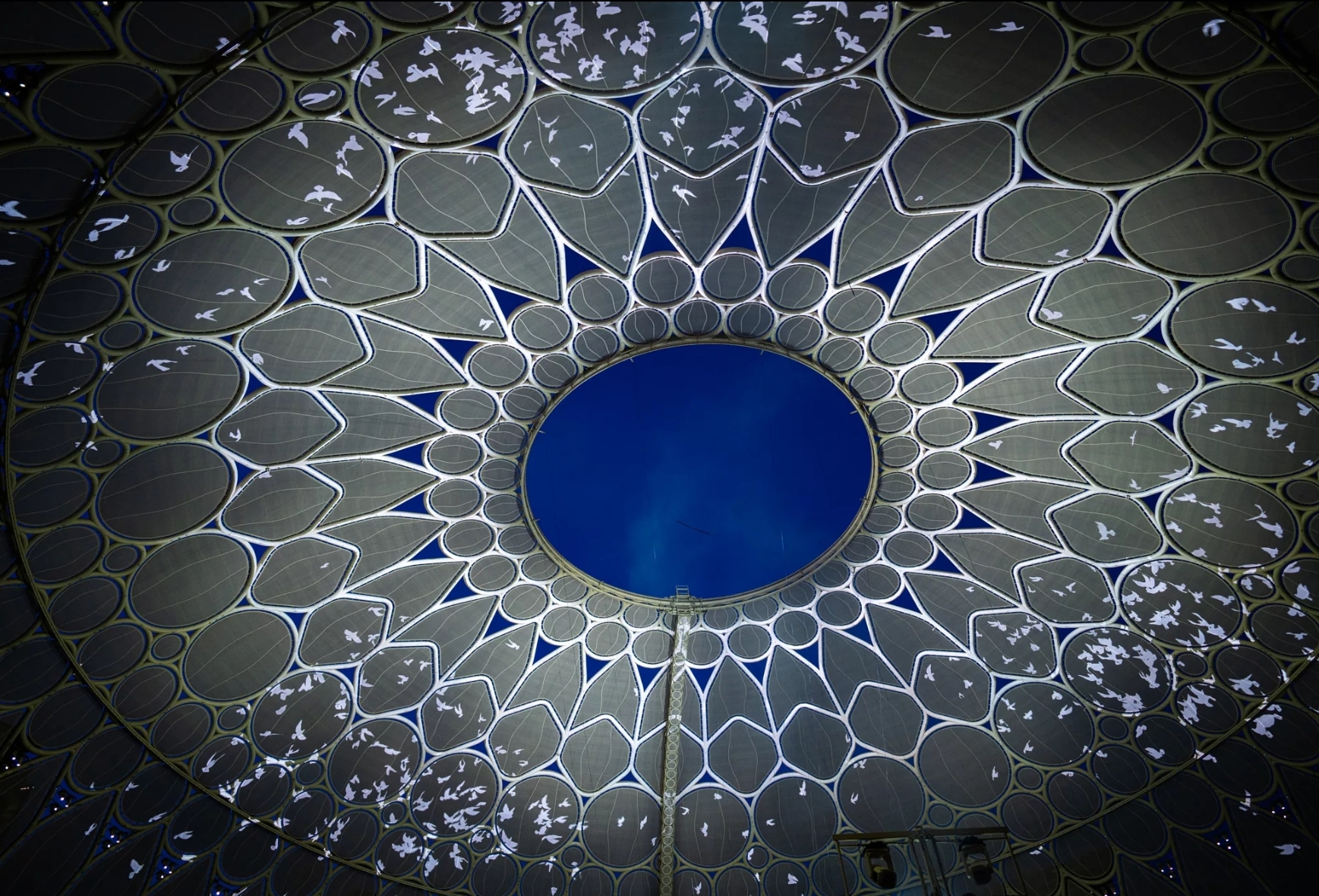
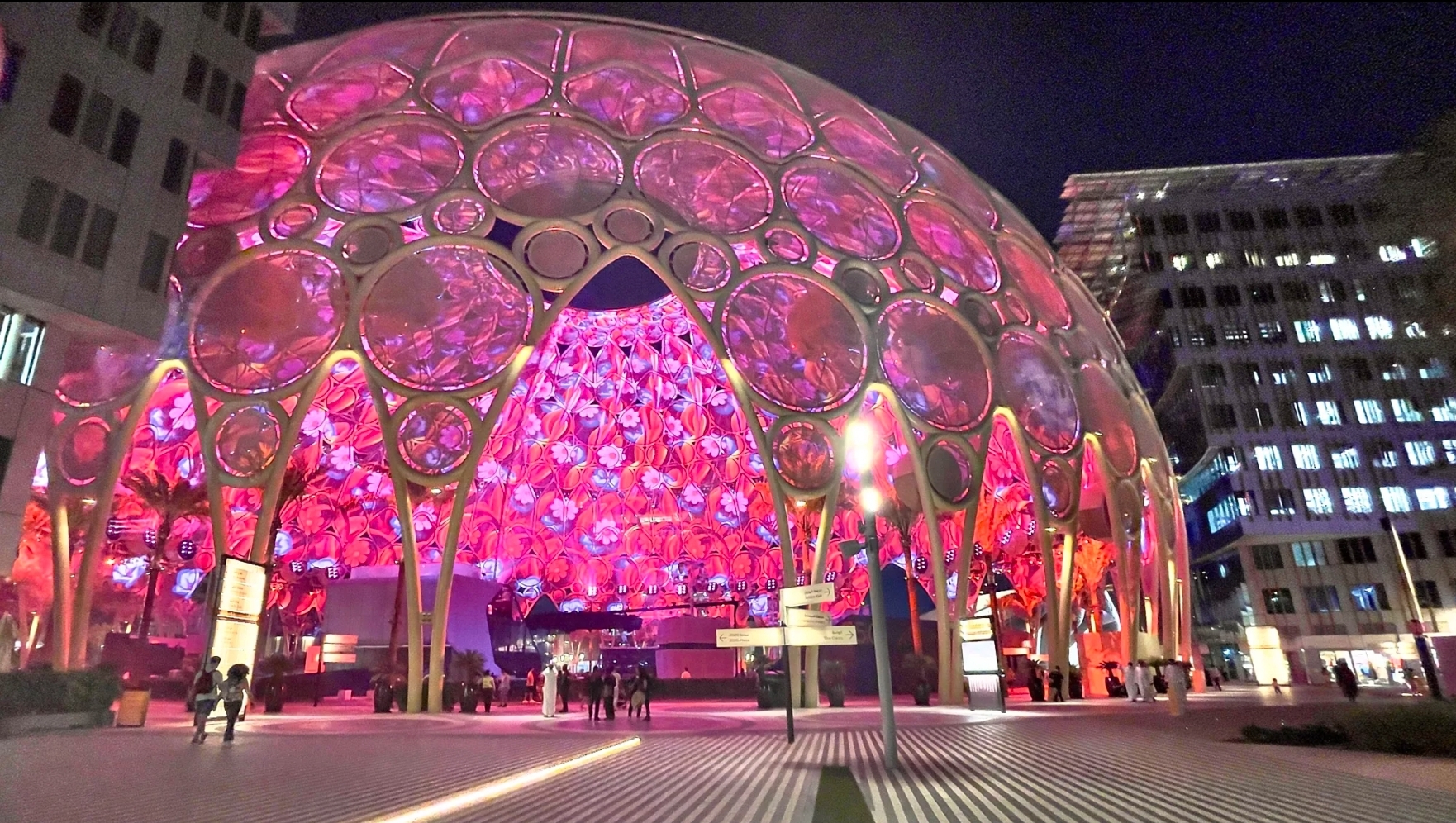