Company:
Lake Shore Boat Top Company, Inc.
Project Details
Fabric 1
Stamoid
Producer:
Serge Ferrari North America Inc.
Supplier:
Trivantage LLC
Fabric 2
Strataglass
Producer:
Strataglass LLC
Supplier:
J Ennis Fabrics
Fabric 3
YKK
Producer:
YKK USA
Supplier:
Trivantage LLC
Fabric 4
Tenera Thread
Producer:
Gore
Supplier:
Trivantage
Design Name
Rob Kotowski, Bob Kotowski
Design Company
Lake Shore Boat Top Company, Inc.
Fabrication Name
Rob Kotowski, Bob Kotowski, Gregory Phillips
Fabrication Company
Lake Shore Boat Top Company, Inc.
Project Manager Name
Rob Kotowski
Project Manager Company
Lake Shore Boat Top Company, Inc.
Installation Name
Rob Kotowski, Gregory Phillips, Nick Featherstone
Installation Company
Lake Shore Boat Top Company, Inc.
Please describe the project specifications
On this yacht enclosure we used Stamoid Top White fabric and 60 Mil Strataglass to provide a rigid tight track-to-track enclosure. Clean lines were key to making this project “POP”! All view lines, zipper breaks, and cover flaps all pickup lines from this boat inside and out to provide a sleek appearance. The previous enclosure was a 5 section window set and we changed this enclosure to a 3 panel enclosure to provide the customer the
“Ultimate View” and not have any visibility issues with zipper breaks in the middle front windshield.
What was the purpose of this project? What did the client request?
Clean cut straight lines for this project was the requirement. The customer’s previous enclosure was a disaster. (Breaklines were all over the place and view lines were too low. The customer also wanted an easy way to remove and install his windows). We raised the view line of the glass so that it was in line with the inside hard top rails. We applied zippers on the bottom of the windows and up the arch so it would be easy for the customer to install and remove. The view inside this boat looking out, is like not having any windows in the cockpit. The clarity is amazing!
What is unique or complex about the project?
This job did not allow room for any errors being that it was tracked to the hardtop, the bottom with zippers of the windshield and up the arch with zipper attachments. Patterning this job with an aftermarket hard top made it very difficult, especially to pattern these windows on the top edge where awning molding PVC track was installed. The powder-coated rails were in the way of a standard track-to-track patterning application. To adapt to this unique situation, we stitched small pieces of screen onto kedar welt to allow us to pin our templates in areas that were not accessible.
What were the results of the project?
Visibility to be seen for miles was the final result! This project by far was one the most enjoyable final results we had this season. If you saw what this boat looked like when it came to our service well and how it left, it was night and day. Because of the excellent results of this front enclosure project, he is currently on our schedule to re-design the aft end of his boat this upcoming Winter/Spring 2016. We have set the bar with the seamless design, and will continue to provide our standard level of excellence!
Content is submitted by the participant. ATA is not responsible for the content descriptions of the IAA award winners.
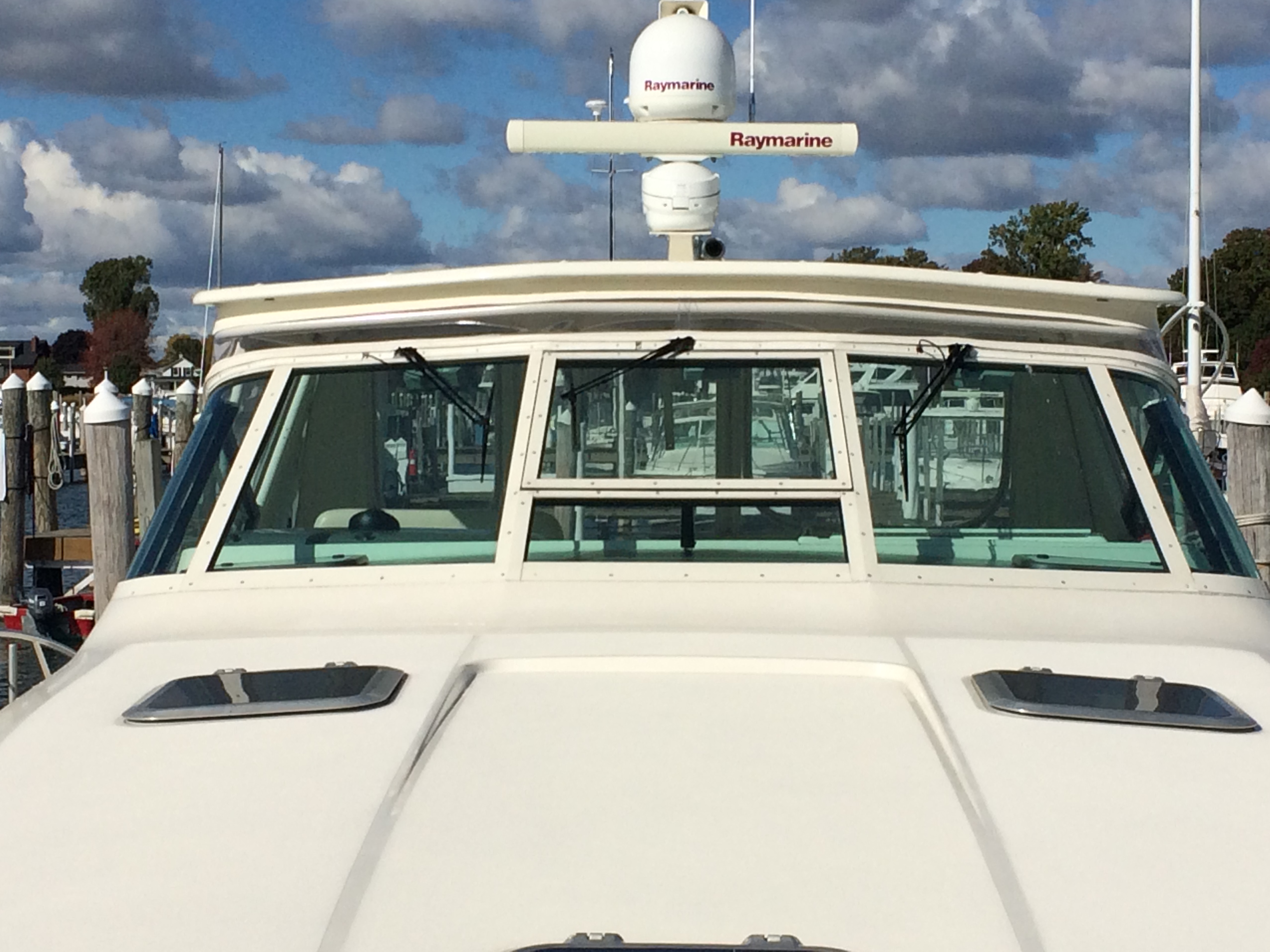
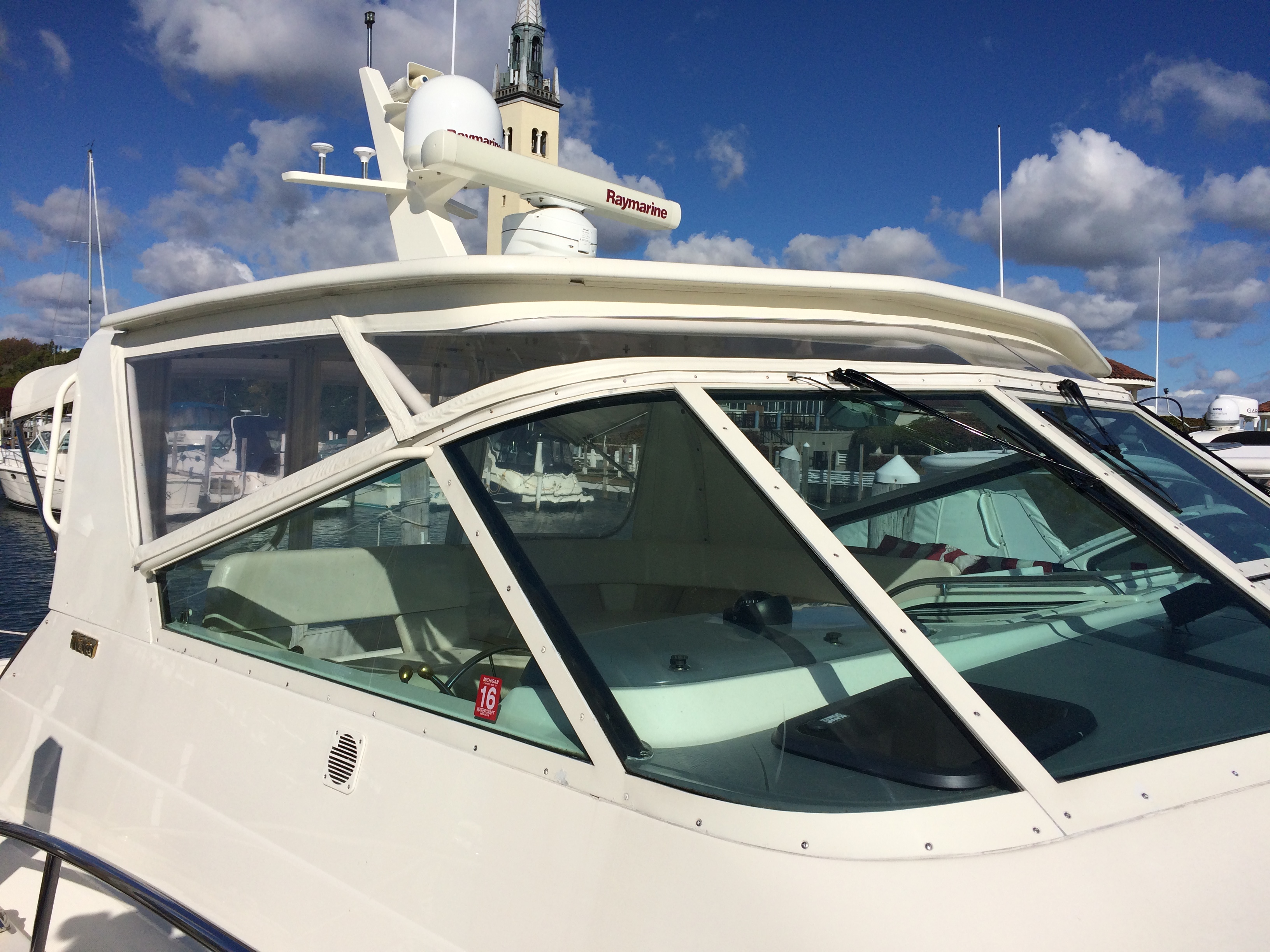
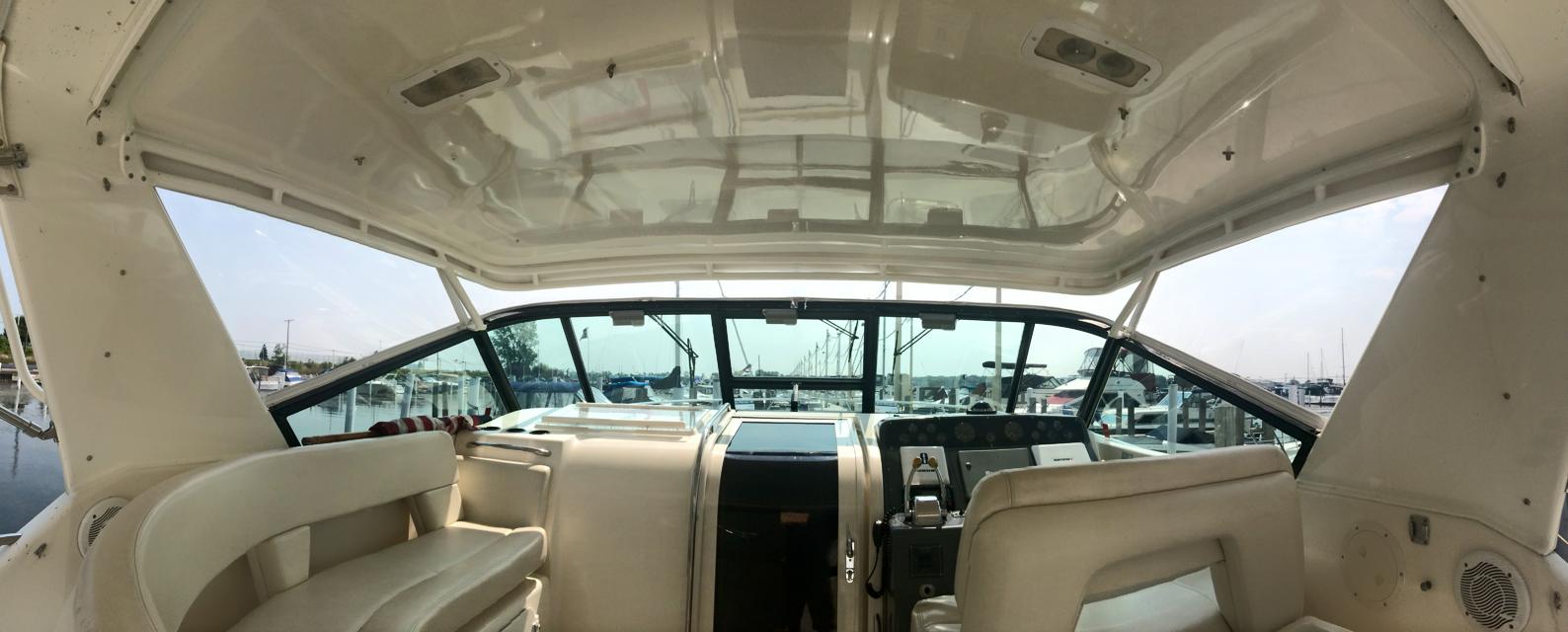
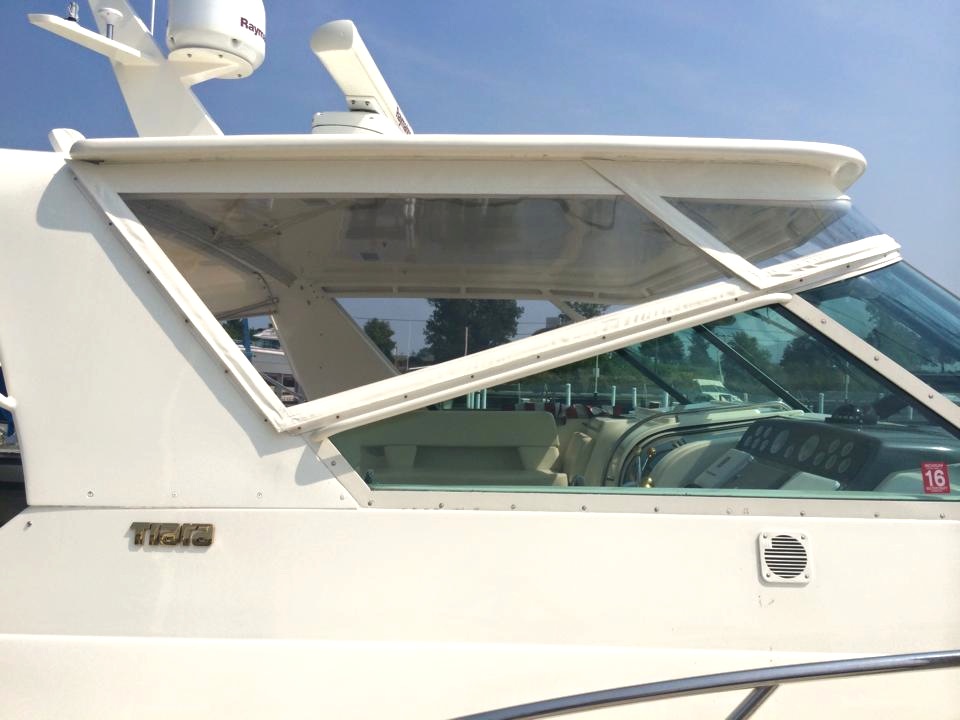