Company:
Fabritecture (UFS Australasia Pty Ltd T/A Fabritecture) Gold Coast, QLD
Project Details
Fabric 1
ETFE
Producer:
AGC
Supplier:
AGC
Engineer Company 1
Maffeis / Seele Covertex
Design Company
Fabritecture
Architect Company
ARM Architecture
Subcontractor Company
Fabritecture
Project Manager Company
Fabritecture / Leighton Contractors
Installation Company
Fabritecture
Please describe the project specifications
The project was a design and construct contract of an ETFE ferry terminal as part of the Elizabeth Quay upgrade development. The canopy was created to provide shelter for passengers embarking on the TransPerth ferry system to and from the Elizabeth Quay terminal.
The aim of the Elizabeth Quay project was to transform the promenade into a culturally stimulating environment for the public. The investment in the redevelopment of Elizabeth Quay was carried out to create a new face for the Perth CBD.A high emphasis was placed on playground facilities, public transport, retail, performers and street vendors to create a specific ambiance.
The canopy project is located in the Elizabeth Quay inlet at the waterfront of the Perth CBD. The structure is an innovative design combining custom printed ETFE cushions with a unique aluminium cladding system and an LED lighting system. The roof is installed onto concrete pylons over a floating jetty system.
What was the purpose of this project? What did the client request?
The Ferry Terminal project was part of Elizabeth Quay’s complete redevelopment in the Perth City waterfront. The project scope was the complete design and construction of the steel, ETFE cushions, aluminium cladding, and custom artwork by a local artist.
The client requested a unique architectural fabric structure that was to be an iconic edition to the area. The design of LED lighting, electrical, hydraulic and mechanical coordination was also part of our scope.
The client envisioned a structure that was harmoniously adaptive to the surrounding environment, complimenting the many other new features of the area.
What is unique or complex about the project?
This project had many complex and unique challenges. Perth MRA engaged a local artist Penny Bovell to create custom artwork that was to be digitally transferred and printed onto the ETFE cushions. The artwork was a conceptual representation of the wind swept water of the Swan River, originally a painting, which was then converted into a halftone image.
Halftone imaging uses different sizes of round dots create an image from a distance, but just look like different sized dots close up. The spacing of the frit pattern has dual-benefits as it displays the artwork from a distance, yet creates sight and shade from underneath the canopy.
Mapping out the artwork on the frit pattern was an involved and complicated process. All printing had to be aligned during fabrication, to produce the correct effect. Forty-two individual ETFE cushions made up the structure, each with a unique print. This printing was further divided into individual patterns, then printed separately and welded together. Once tensioned, the artwork ended up aligning perfectly and exceeding the client’s expectations.
We value-engineered the original structural system developed by ARUP into the counter-levered trusses. This provided significant savings in steelwork weight.
Another complexity experienced was in combining the steelwork, aluminium cladding panels, gutters, drainage and ETFE into the structure (from a coordination perspective). We had three separate parties create the final 3D workshop model. This model was divided into three disciplines: steelwork, cladding, and ETFE. The model was then overlaid to guarantee the Buildability and fit-up.
By 3D modelling all components parallel with the detailed design, we were able to ensure no clashes were created, and that everything was going to work.
3D modelling was also used to map and model all services reticulated within the structure. The internal drainage, electrical wirings, ETFE air supply system, lighting drivers, and communications and sensors for the ETFE were all concealed within the structural steelwork.
Setting the air-handling system of the cushions carried considerable associated risks. The system was used as a temporary measure while the surrounding infrastructure was completed. It was this surrounding infrastructure that would eventually be used to house the BIM system that monitors and controls the cushions.
The aluminium cladding system was another incredibly complicated element. The final design comprised of over 500 different aluminium panels that were documented on over 800 shop drawings. The aluminium cladding system was used to create the 23 different architectural fins that clad the trusses. These fins also clad the central spine of the structure.
The installation was compressed into a limited schedule, which increased the amount of equipment required on site and meant labour had to work simultaneously on different tasks. The schedule was tight due to the works in surrounding areas. We were racing against the excavation and flooding clock, meaning that if we didn’t complete the work on time, we would be forced to stand down while they flooded the inlet. We would then have to complete the rest of the work from barges on the water.
There were many different components included in the structure that had to be delivered within this tight program. The excavation occurring around the site further emphasised the importance of staying on schedule as they were literally digging us out of our own workspace.
The single counter levered structural I beam and plate arms were originally meant to be incorporated. Value-engineering highlighted the opportunity for a new solution that could make the structure lighter and ergo more cost-effective. This solution was to completely redesign and incorporate a truss system.
The design points of the canopy were the large columns on wide centres (9M) supporting a large structural spine that the truss arms counter-levered from, these truss arms were hidden using aluminium cladding that was very complex to incorporate. The coordination of the plenum air handling/duct system was an intricate part of the ETFE cushioning system which was all contained within the structural spine.
What were the results of the project?
The end result is an incredible piece of fabric architecture with a unique artwork that is a tribute to community. The structure utilises a state-of-the-art ETFE cushioning system. The structure itself is a piece of artwork protruding from the water, and was delivered successfully on time and on budget.
The complicated lighting, plenum and hydraulic system is efficiently hidden by the structural design of the aluminium fin plate cladding system, to create a flawless, dynamic finish.
The Elizabeth Quay Ferry Terminal is an exciting addition to our ETFE portfolio.
Content is submitted by the participant. IFAI is not responsible for the content descriptions of the IAA award winners.
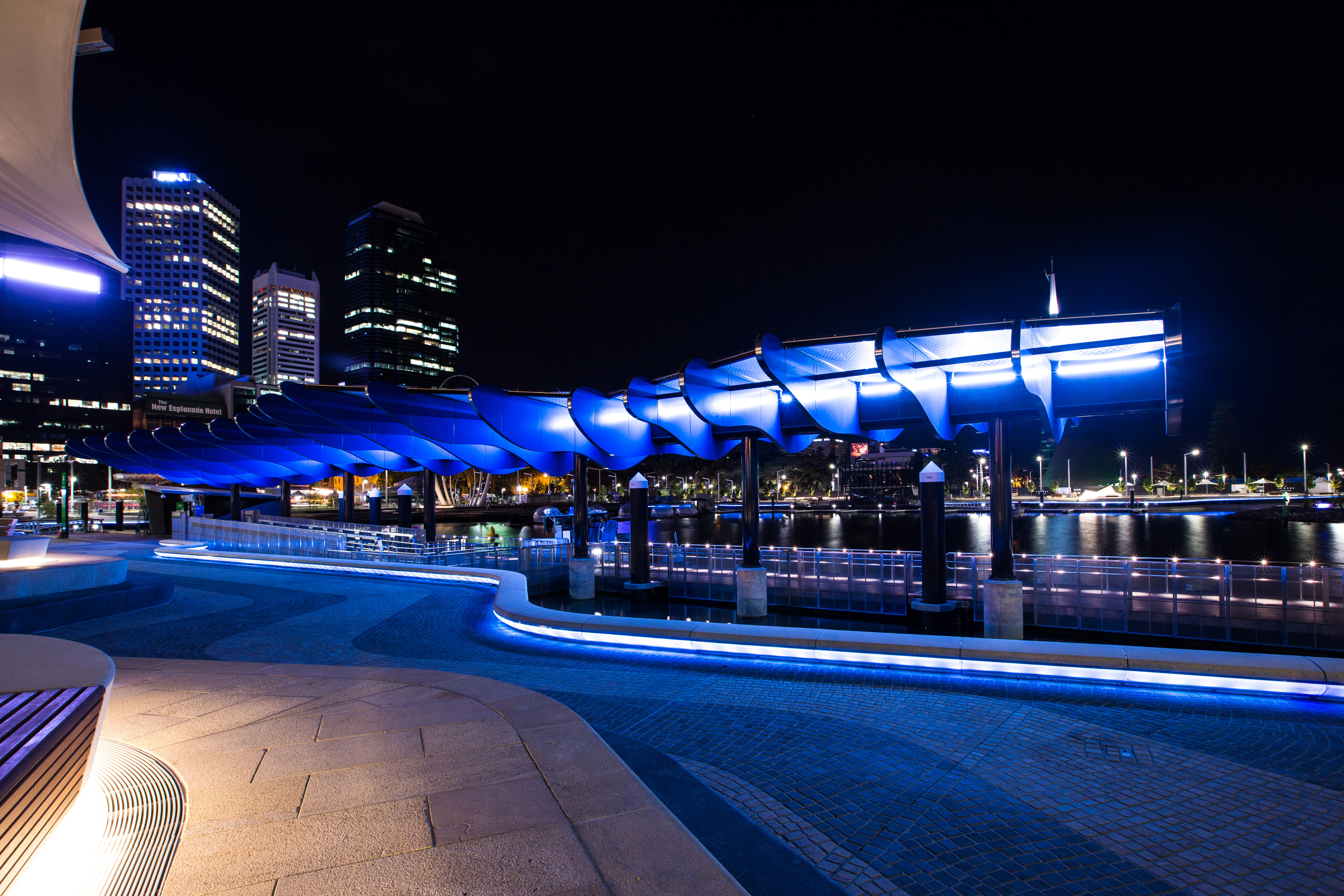
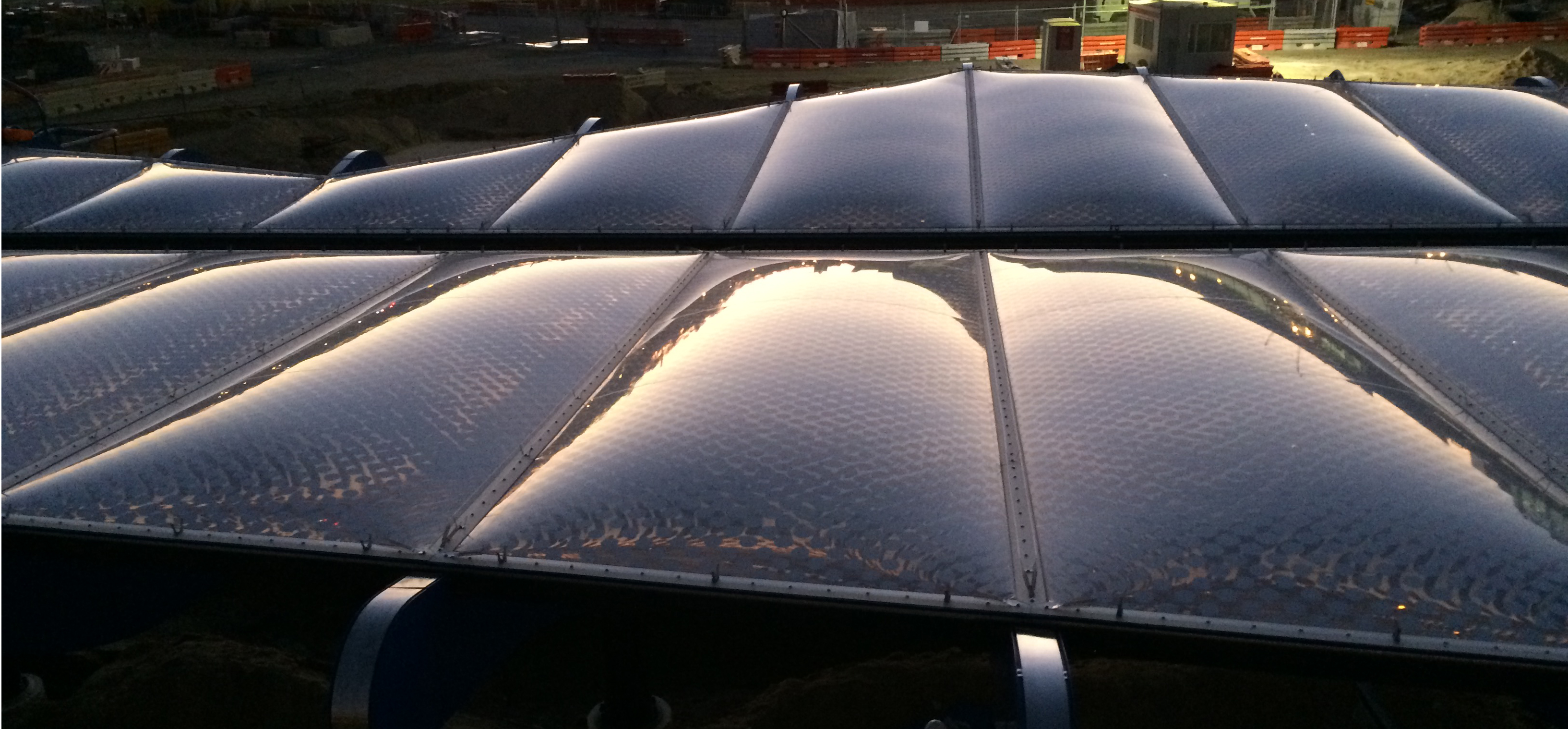
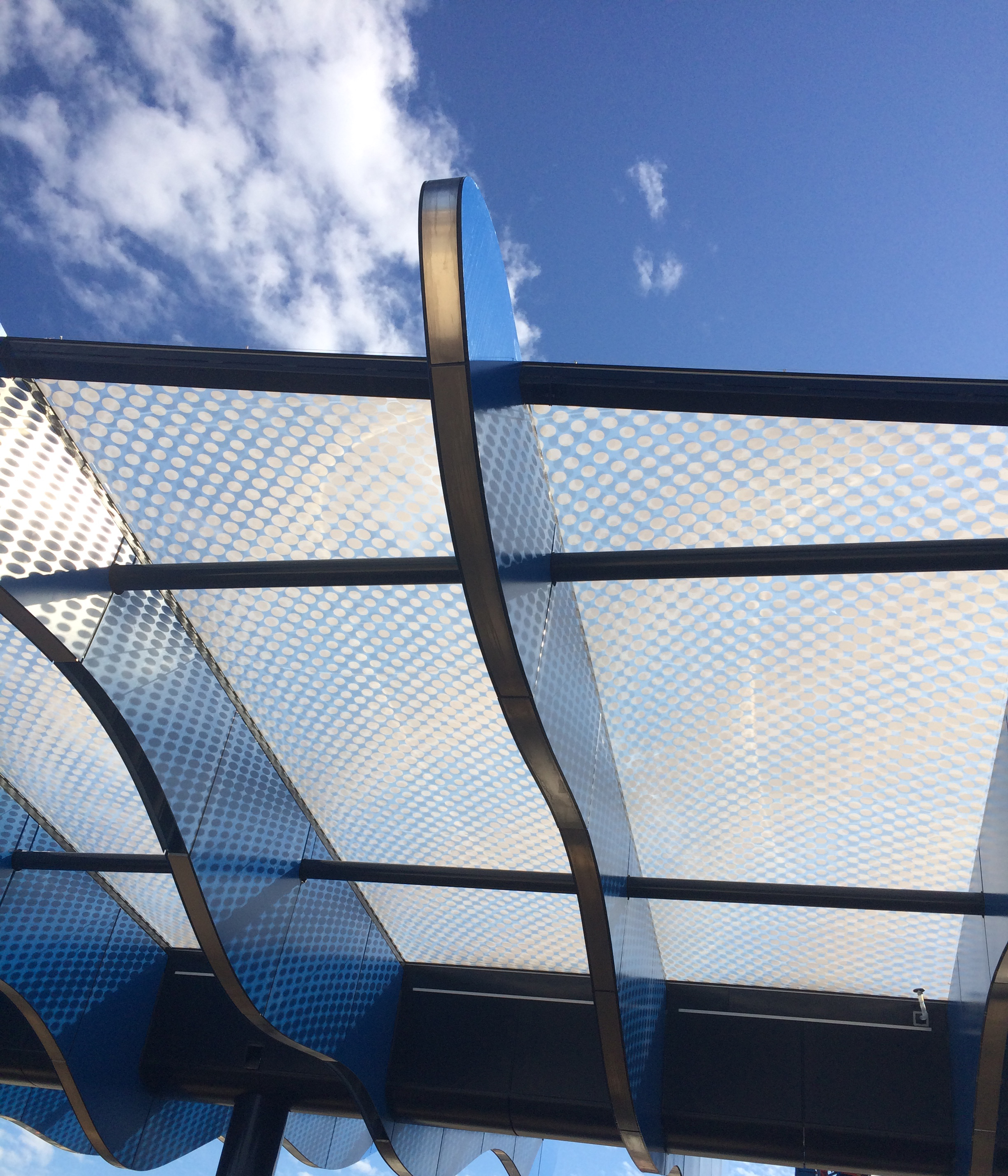
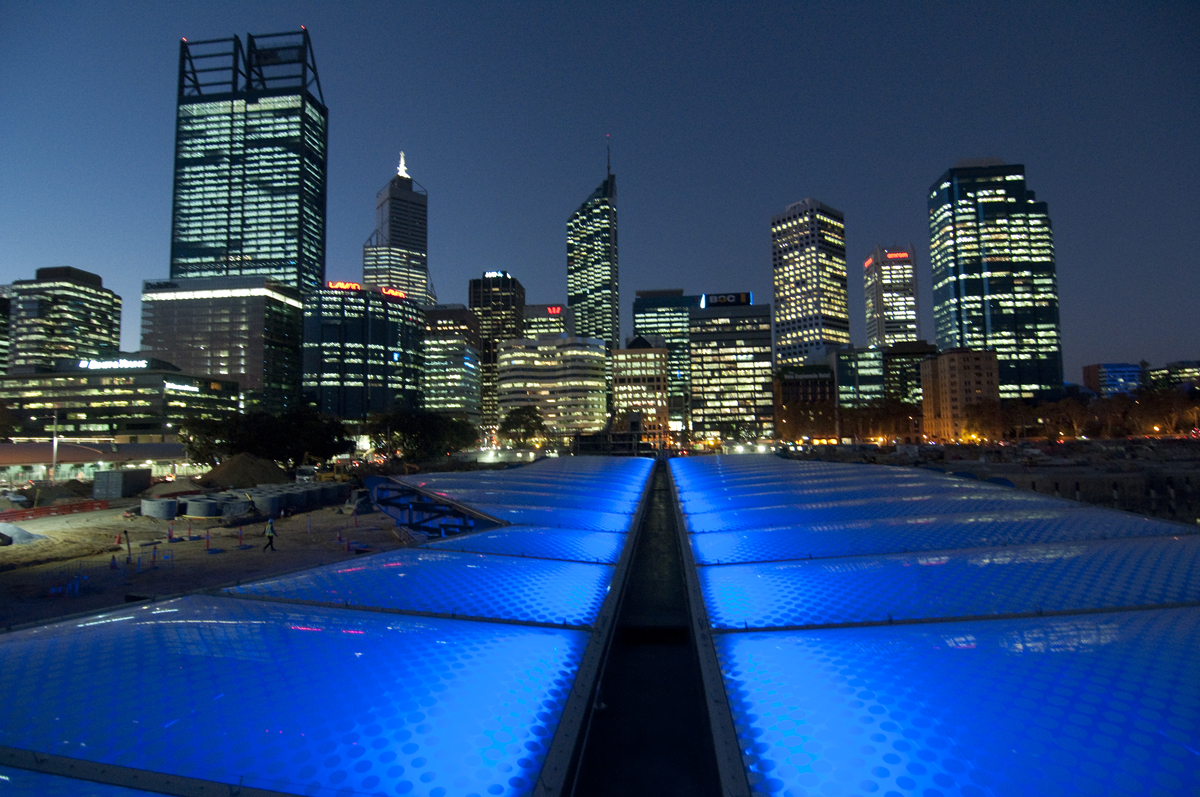