Company:
Signature Structures
Project Details
Fabric 1
702
Producer/Manufacturer:
Serge Ferrari North America Inc.
Primary Use:
Main Fabric
Engineer Name 1
Dirk Cos
Engineer Company 1
Lightweight Design
Design Name
John Dufal
Design Company
Signature Structures LLC
Architect Name
Signature Structures
Architect Company
Signature Structures LLC
Fabrication Name
Lightweight Manufacturing
Fabrication Company
Lightweight Manufacturing
Subcontractor Name
Signature Structures
Subcontractor Company
Signature Structures LLC
Project Manager Name
Signature Structures
Project Manager Company
Signature Structures LLC
Installation Name
Signature Structures
Installation Company
Signature Structures LLC
Please describe the project specifications
The Junior Tennis Champion Center is an award winning world class training center for young athletes. The centerpiece of their College Park facility has always been their 12 indoor courts housed in three connected tension fabric structures. After two decades, the original membrane had come to the end of its useful life.
The club wanted to refurbish the membrane on all three structures, and while doing so change the color scheme of the structures from a standard white roof/tennis green sidewall common for tennis structures. We provided an aluminum colored membrane for the roof with a blue sidewall to better reflect the club's colors.
The project was a massive undertaking with three (3) 31,200 square foot structures with two membrane covered connecting structures and a connection to a conventional structure.
Due to both installation challenges and the club's desire to minimize disruptions to the interior of the structure, We utilized its unique over the top method of fabric refurbishment, which features the installation of galvanized steel brackets & hardware for panel securement to intermediate arches and fabric panels featuring pockets manufactured along length (tension to endwall/adjacent panel) Includes manufactured flap to seal to adjacent panel. When completed, the cover was seamless and fully tensioned.
We also had to reverse engineer membrane covers and flashing/connections systems for the connecting tunnel relying, as we often do on field measurements and site inspections in lieu of original drawings, which in this case and most other of our refurbishments, were not available.
What is unique or complex about the project?
Our company had been inspecting/maintaining and servicing the structures for this client for years. We had been advising them on the remaining membrane life and helped them plan for the future membrane refurbishment. Thus, the trust and respect between JTCC and Signature that had been built up over time made us a natural partner for the refurbishment.
While we refurbish more membrane covers for more structures regardless of OEM than anyone in the industry, there were several challenges that set this project apart from others. Due to financing and scheduling elements, the client requested a phased install, which required multiple procurement phases and mobilizations. In addition to the size and complexity of the 3-structure complex and the phased production and installation schedules, the fact that the project was conceived, contracted, and completed during the pandemic and all the logistical and supply chain issues that went along with it sets it apart as well.
Content is submitted by the participant. IFAI is not responsible for the content descriptions of the IAA award winners.
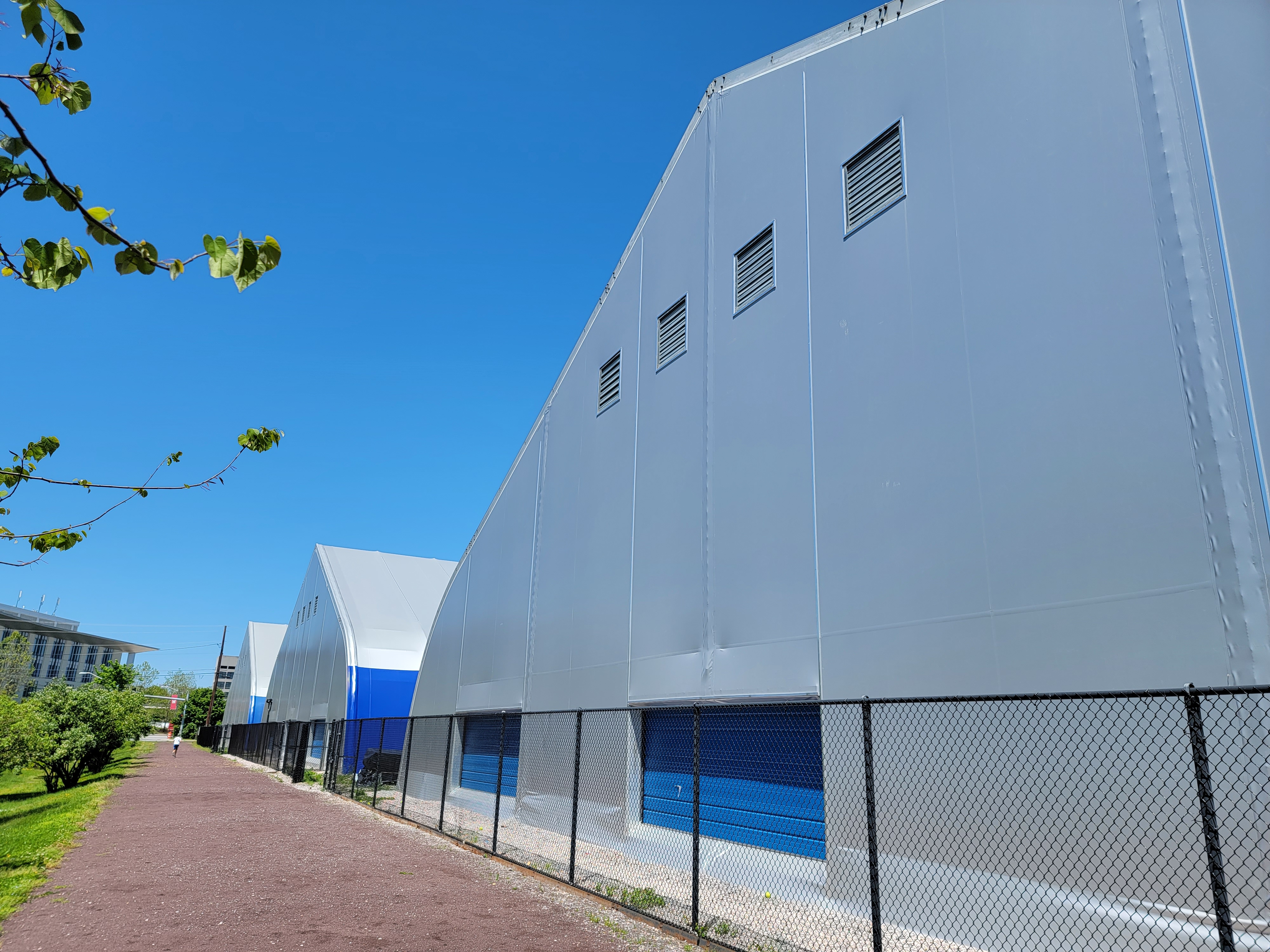
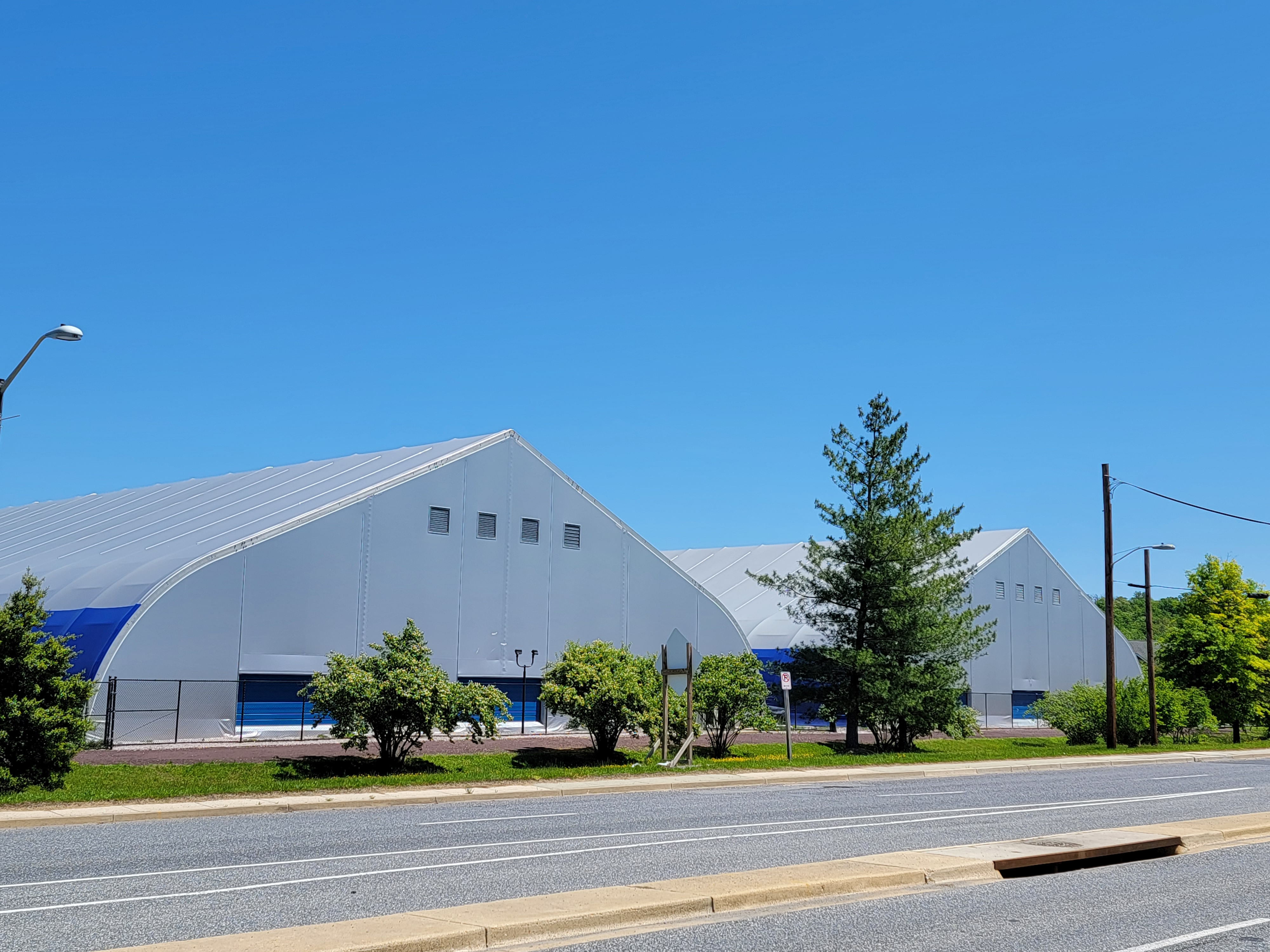
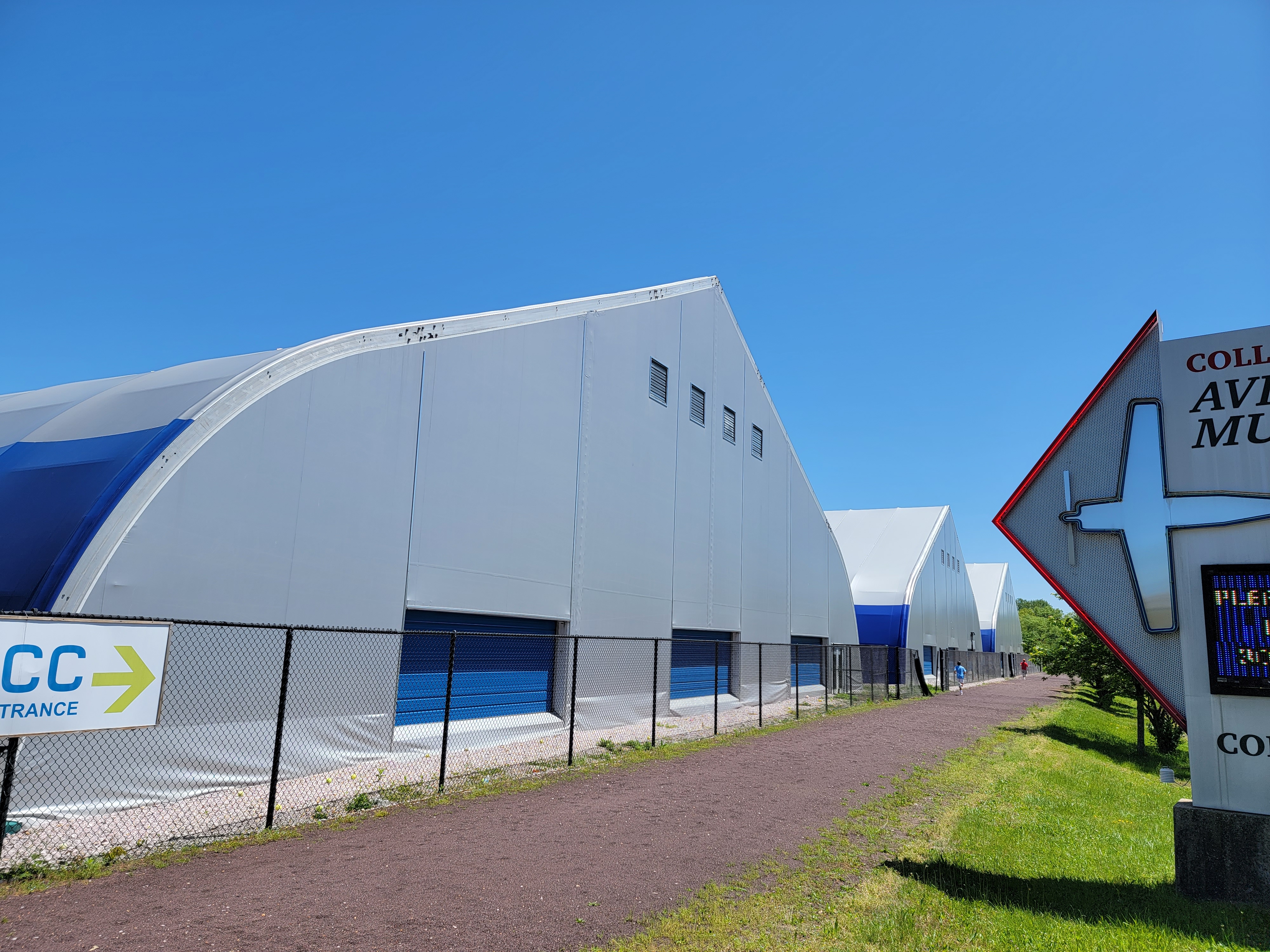
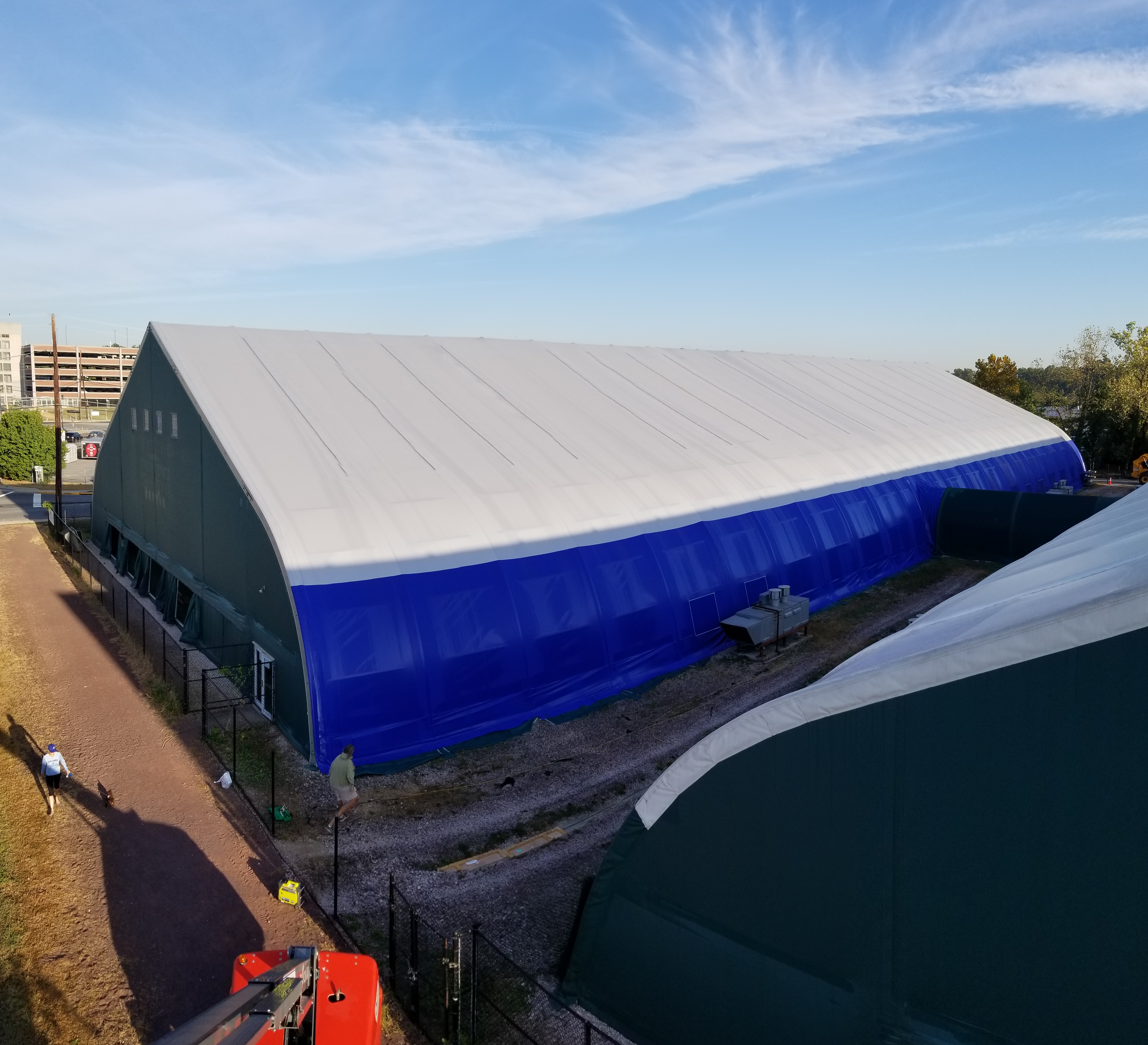