Company:
Shelter Structures Inc. Philadelphia, PA
Project Details
Fabric 1
Précontraint 502
Producer:
Ferrari S.A.
Engineer Name 1
Steve Fatzinger
Engineer Company 1
Lightweight Design
Design Name
Charles Smail
Design Company
Shelter Structures
Fabrication Name
Dirk Cos
Fabrication Company
Lightweight Manufacturing
Subcontractor Name
Richard Isbell
Subcontractor Company
Fabritex
Project Manager Name
Gregory Jones
Project Manager Company
Shelter Structures
Installation Name
Steve LaJoye
Installation Company
Garden Center Maintenance
Please describe the project specifications
The project specifications originated with an innovative environmental technology group that needed help designing a series of state of the art Organic Recycling Facilities for the state. According to the group’s sponsor, only our Company was able to rise to the challenge of helping them design and deliver an innovative and cost effective shelter that made it possible for their patented technology and process to achieve optimal performance. Critical design considerations included process flow geometry, heavy equipment operating clearances, airflow and humidity control and state building code requirements for permanent structures in a high wind zone.
Selected Specifications:
o Shelter "A", Mixing/Receiving Building – 134'W x 100'L x 46'H – 13,400 ft2
o Shelter "B", Composting Building – 134'W x 270'L x 40'H – 36,180 ft2
o Shelter "C", Canopy Building – 134'W x 100'L x 38'H – 13,400 ft2
o Rolling Service Doors - 4 @ 18'W x 18'H
o Personnel Doors - 3 @ 36"W x 80"H
o Louvers - 3 @ 15'W x 10'H, 5 @ 15'W x 8'H
o Fans - 6 @ 4.8'W x 4.8'H
o 150 MPH wind load
What was the purpose of this project? What did the client request?
Our Client developed a composting technology that enables wastewater treatment operators to significantly reduce costs, improve water conservation and create a sustainable resource used to enhance crop production, reduce contaminants in ground water and ease the economic burden on municipalities by reducing the volume of unusable sewage byproduct produced by traditional water treatment processes. The purpose of this project was to enable our Client to deploy this technology in a cost efficient and profitable way. The Client needed us to help them design and erect a facility that would accommodate and optimize their process flow, control airflow and humidity levels and minimize operating and maintenance costs.
What is unique or complex about the project?
The requirements of our Client's technology and recycling process flow calls for an elaborate foundation system. This necessitated a meticulous design-build effort that called for a bespoke frame and fabric shelter. Once our Company demonstrated how an industrial fabric envelope could provide the solutions they sought, the Client eagerly joined our collaborative value engineering process to develop an optimal design. The Client’s recycling process technology, required process flow for the completed facility, and complex public/private financial relationships imposed some unique and significant challenges. We ensured that the shelter design would facilitate the Client's process requirements and that it would meet the ASCE 7-10 wind loads specified by the state’s building code. Because of the numerous foundation elevation changes required by the foundation system, our Company had to account for exceptionally asymmetrical reactions at the truss anchor points. Trusses were anchored to stem walls of various heights and widths, a concrete processing section roof twenty feet high, and even some points below grade; the final design required fifteen different anchoring designs. Penetrations necessitated by the large louvers and fans integral to the Client's process, required our team to design a variety of sidewall tension systems to ensure that the fabric would lay properly and provide a tight seal. Furthermore, heavy equipment operating clearances, airflow and humidity control needs demanded that the shelter sections have different peak elevations and separation. We designed a special stem wall closure panel and a unique fabric transition panel to seal gap between sections while keeping the exterior envelope continuous to prevent water intrusion. Due to Client financial commitments the installation schedule was highly compressed and demanded that both Company and Client project management teams work closely to coordinate the simultaneous efforts of multiple construction trades. To help our Client realize their vision as quickly and economically as possible, we provided consultative support to the Client’s Construction Site Manager well beyond what a typical shelter installation project would require.
What were the results of the project?
The primary result of this project was to enable our Client to deploy their innovative recycling technology profitably, both in terms of financial benefit for our Client and globally by enabling municipal wastewater treatment operators to transform a previously unusable waste byproduct into a safe, sustainable and environmentally beneficial product in an affordable and even profitable way. Our Company focused on understanding and fully defining our Client’s needs. We applied our Value Engineering Method to design a system of shelters that optimized interior volume to achieve a safe and efficient process flow, provided the airflow and humidity control necessary for our Client’s process and reduced facility operating and maintenance expenses. By seamlessly adapting our frame and fabric envelope to the foundation system, we further reduced the Client’s total engineering costs. Strategic use of light transmitting fabric allowed natural light to illuminate the interior, reducing the need for electric lighting. Finally, the design provided our Client the reassurance of an IBC-compliant permanent shelter certified to ASCE 7-10 Risk Category II standards that can be replicated anywhere, thus allowing them to benefit from economy of scale. Ultimately, this project will enable the Client to establish a profitable business model that is highly desirable and affordable for its municipal partners. This is the second facility we've built for this customer, and our company’s commitment to value engineering has earned us the opportunity to work with the Customer to design a completely new organic processing facility.
Content is submitted by the participant. ATA is not responsible for the content descriptions of the IAA award winners.
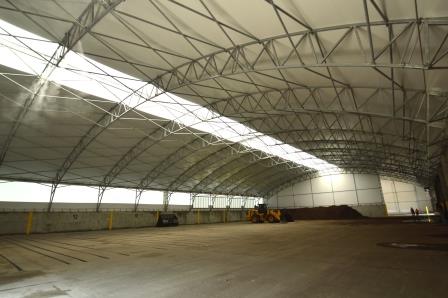
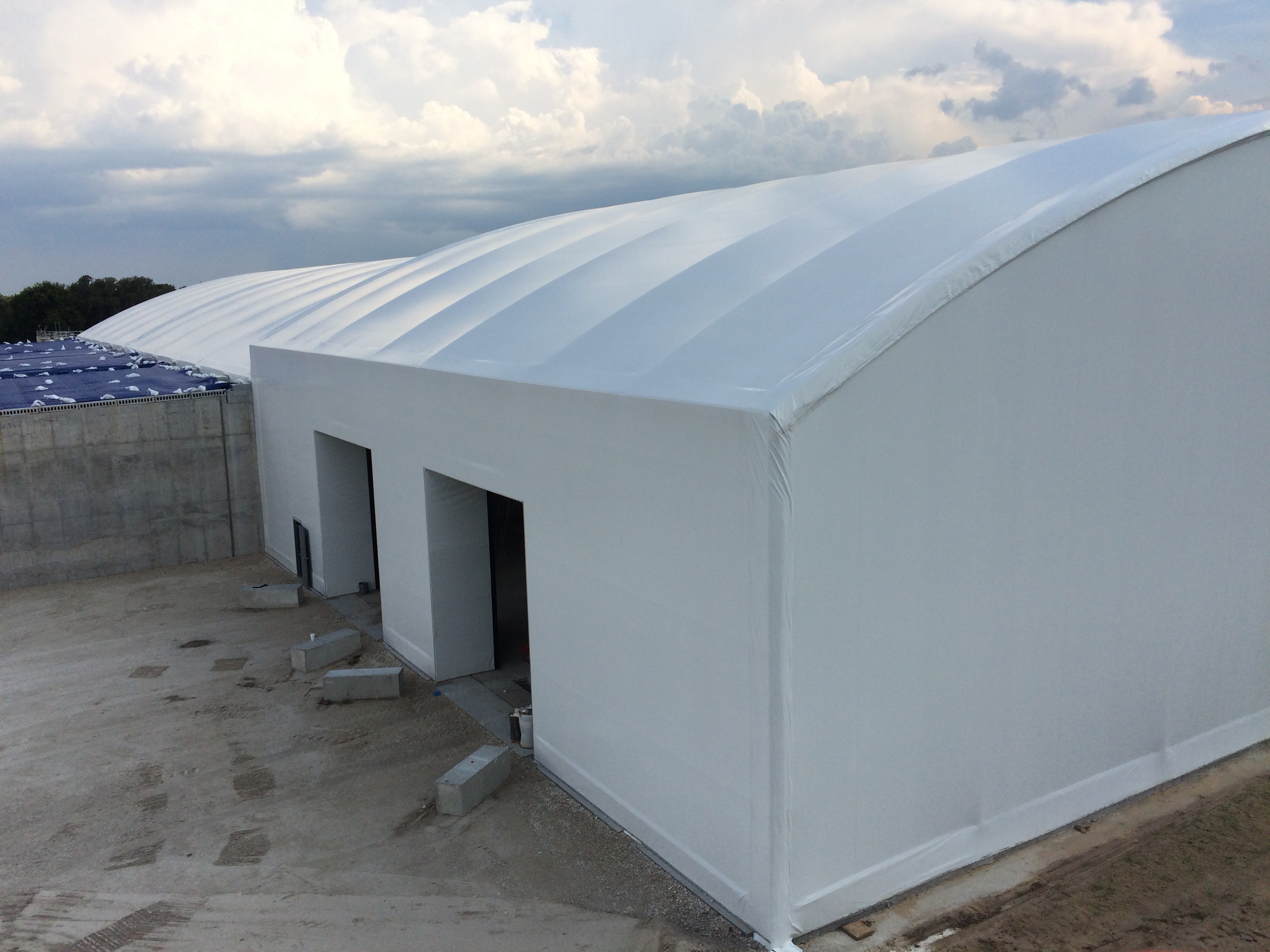
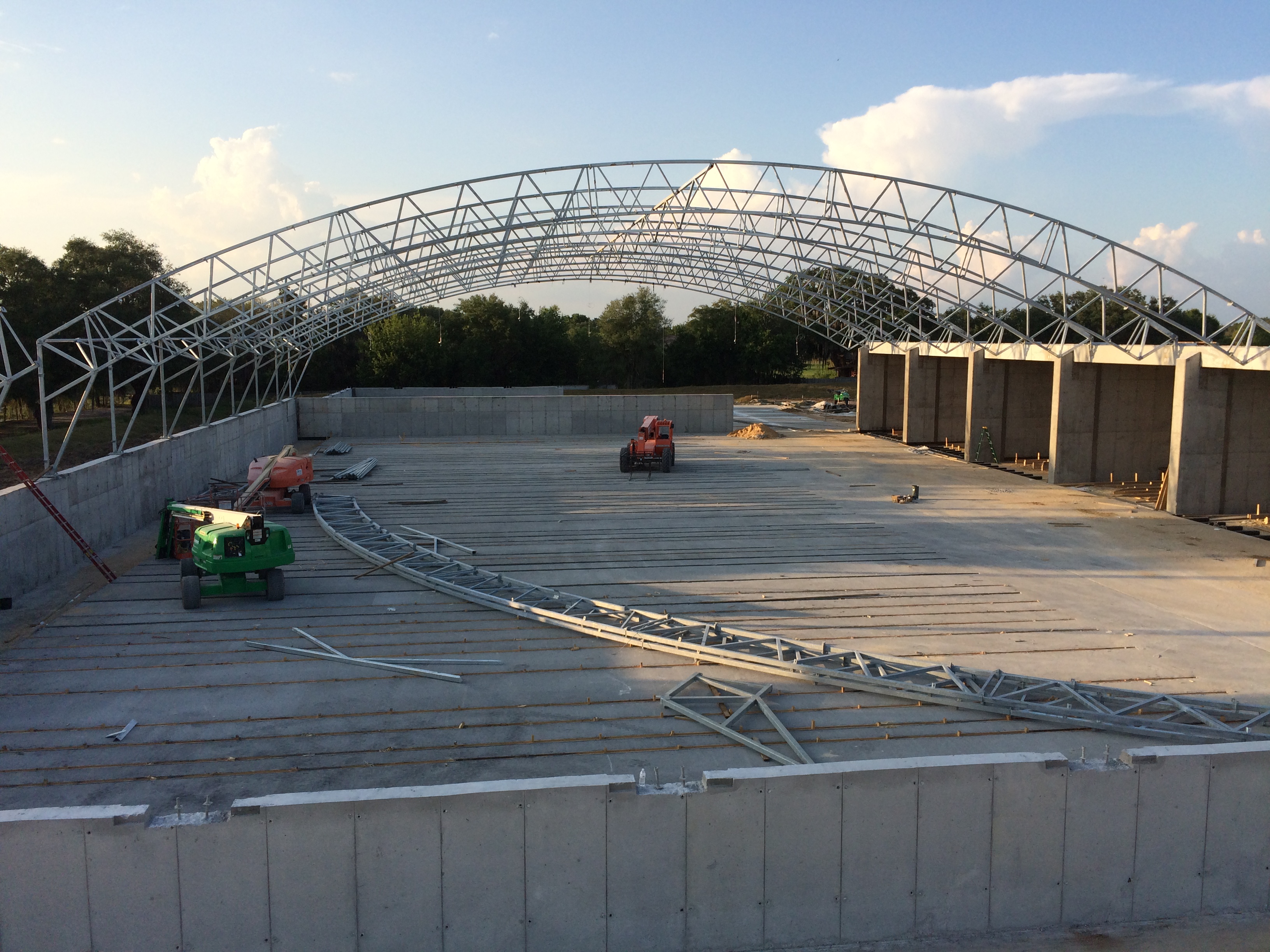
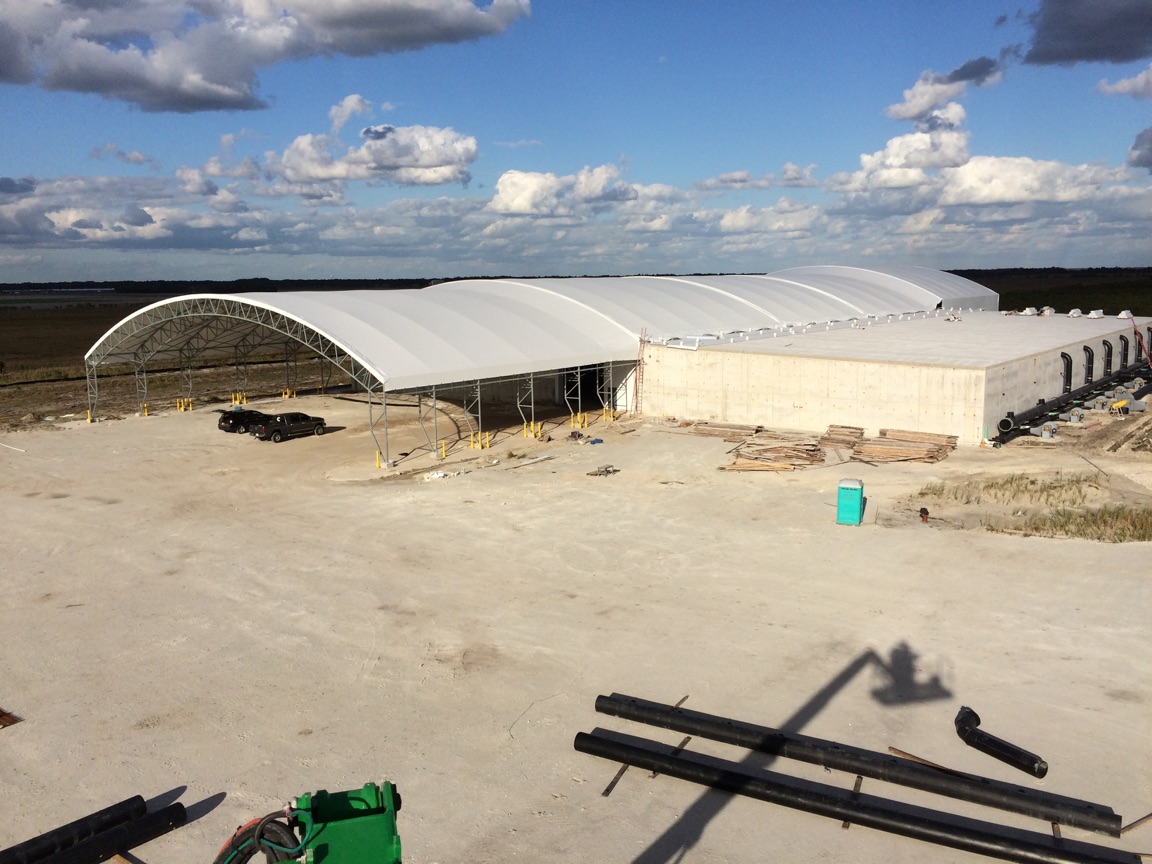