Company:
TenCate Geosynthetics Americas Charlotte, NC
Project Details
Fabric 1
Geotube®
Producer:
TenCate Geosynthetics
Engineer Company 1
Geosyntec
Design Name
Meena Viswanath and Ming Zhu
Design Company
Geosyntec
Fabrication Company
TenCate Geosynthetics
Subcontractor Company
Infrastructure Alternatives
Project Manager Name
Kirk Foley
Project Manager Company
Infrastructure Alternatives
Installation Company
Infrastructure Alternatives
Please describe the project specifications
Because of the new federal EPA regulations concerning the management of Coal Combustion Residuals (CCR), a Virginia coal fired power plant was required to start shutting down their wet fly ash lagoons. However, to keep the plant in operation as they switched from the wet process to the dry process, they were required to build a dam across the middle of the primary lagoon to create a dry stacking area on one half of the lagoon. This required removal of 66,000 m3 of contaminated CCR from the wet half of the lagoon to keep the plant in operation during the changeover. As a beneficial use, the 66,000 m3 of contaminated sediments were dredged and contained and dewatered in the 3,650 lin. meters of 13.7m circumference Geotube® units to construct the required dam. By using the Geotube® technology, no additional materials were required to be imported to build the dam.
(12,000’ (3,660m) of 45’ (13.7m) circumference Geotube® containers)
What was the purpose of this project? What did the client request?
To construct a 12’ (3.65m) high dam to act as a gravity retaining structure to separate the wet side of a coal ash lagoon from the dry side. What did the client request?: The dam must be a stable structure and be constructed without any interruption of the operation of the power plant.
What is unique or complex about the project?
The unique aspect of this project was the beneficial use of fly ash sediment (CCR) contaminated waste material that was dredged in slurry form from the lagoon into the Geotube® containers that were 45’ (13.7m) circumference x 200’ (61m) long. The individual tubes were placed side by side and end to end in a two layer 3 – 2 pyramid configuration to form the continuous 2,400’ (730m) long dam.
What were the results of the project?
In total, 80,000 yd3 (61,000m3) of the CCR was dredged from the lagoon to form the dam. The project took 36 days with 430 hours of dredging time for an uptime efficiency of 99.3%. The CCR slurry consolidated to 80% dry solids inside of the Geotube® containers. The client was totally satisfied because the Geotube® dam was constructed with a large volume of waste material without a single minute of interruption of the power plant operation.
Content is submitted by the participant. IFAI is not responsible for the content descriptions of the IAA award winners.
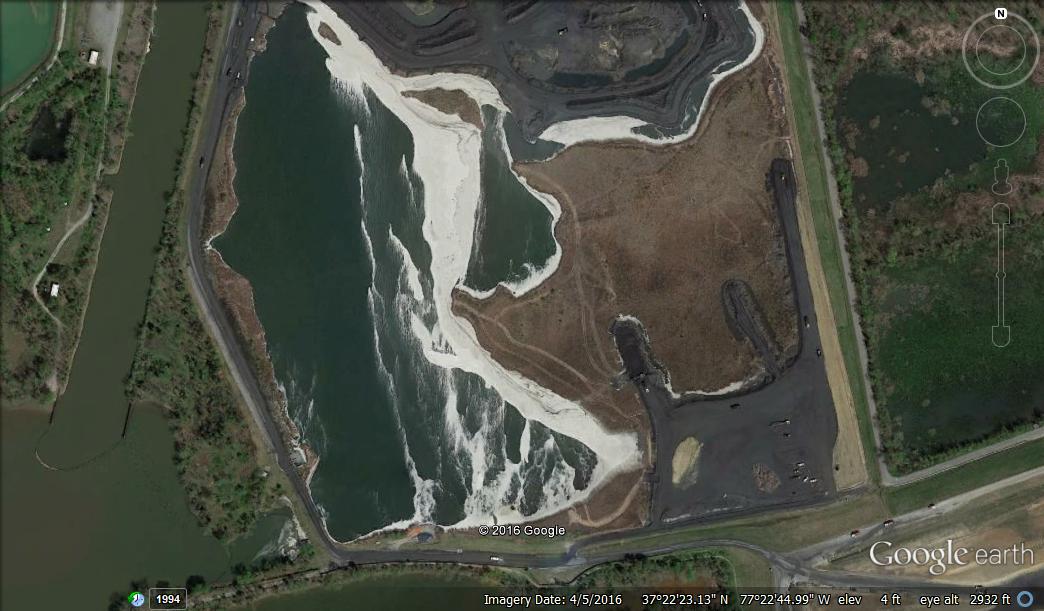
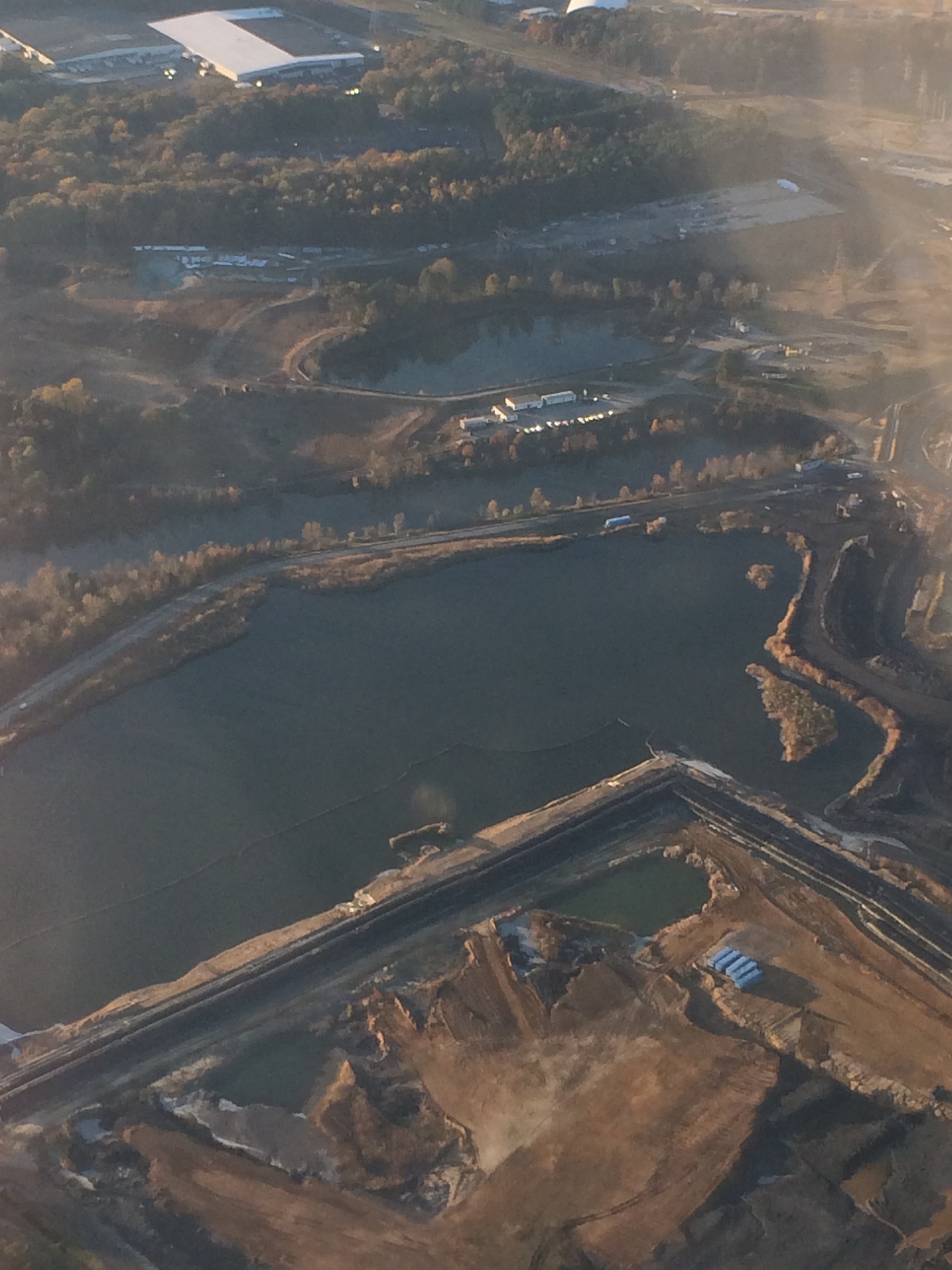
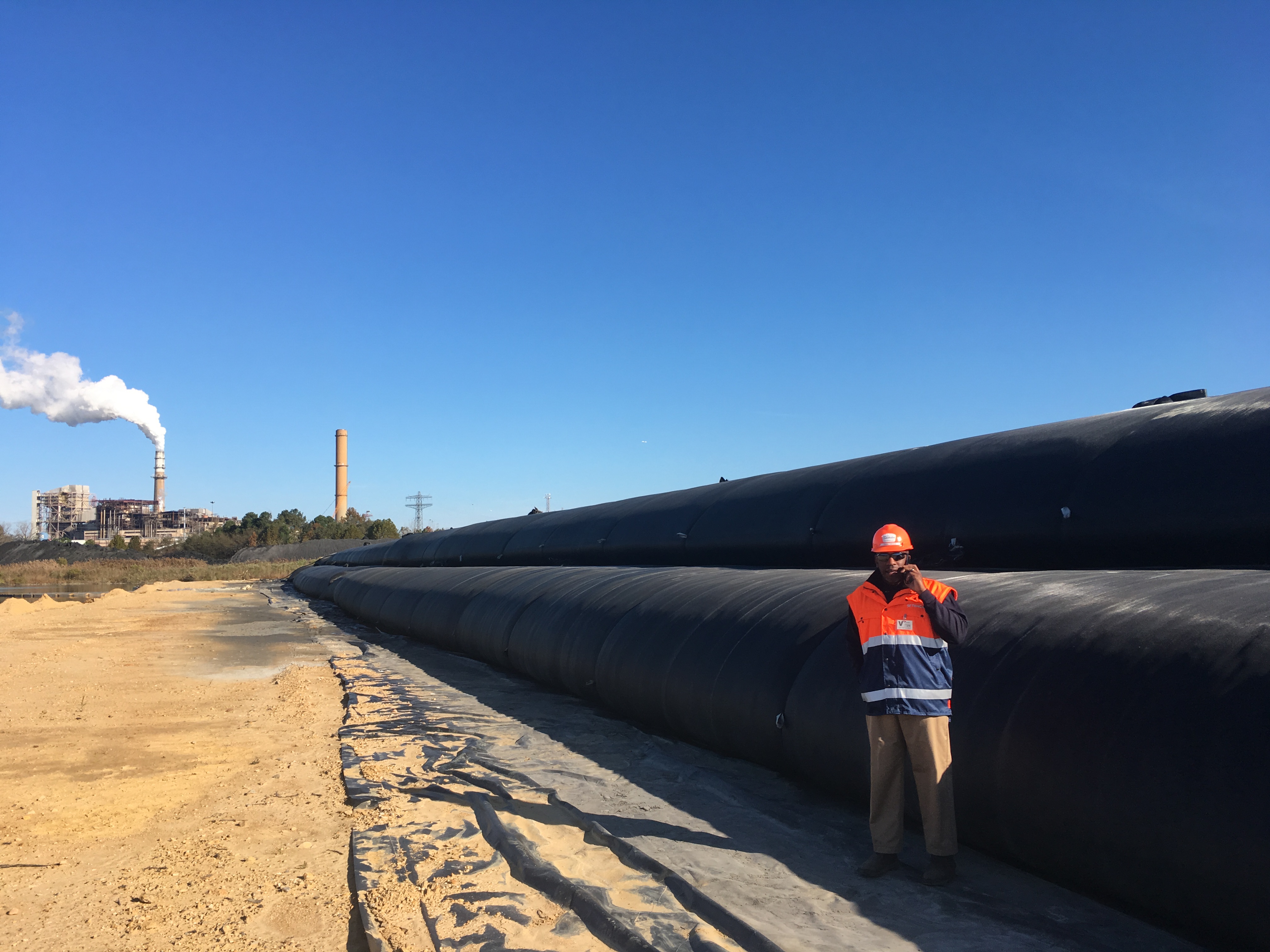
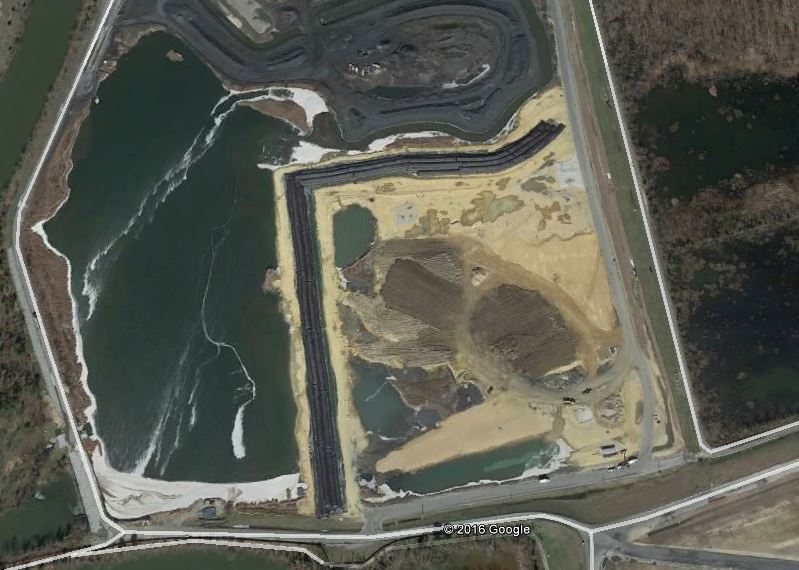