Company:
TenCate Geosynthetics Americas Pendergrass, GA
Project Details
Fabric 1
Mirafi
Producer:
TenCate Geosynthetics
Supplier:
TenCate Geosynthetics
Engineer Company 1
Barr Engineering
Subcontractor Company
Wanzek
Installation Company
Phillips & Jordan
Please describe the project specifications
This project is the construction of the first commercial-scale wind farm in North Carolina. It was for a renewable power generation facility providing clean energy. For the construction of wind farm, subgrade stabilization & reinforcement was necessary for the construction of 60+ miles of access roads to erect 104 turbines.
What was the purpose of this project? What did the client request?
The contractor was responsible for constructing over 60+ miles of access roads for the 104 turbines in the first phase of the Desert Wind Farm project.
What is unique or complex about the project?
The access roads were the only source of entry, they had to support construction traffic over soft, wet North Carolina farmland soil. The access roads were used by aggregate and concrete trucks, delivery tractor trailers (with heavy turbine components) and for moving the cranes between the wind turbines. The original design specified geogrid with 10” of Dense Graded Aggregate (DGA). The subsurface investigation revealed that the in-situ soils consisted of peat and organic clays with a CBR value as low as 0.7% and silty/clayey sands with a CBR value of less than 4.0%. From the start of the project, the grading contractor had trouble with the roadways being too saturated. Multiple attempts at stabilizing the subgrade with geogrid were unsuccessful. The only way to stabilize the roads was to add additional stone. However, the aggregate imported by railcars was very expensive. The contractor tried cement stabilization as an alternative, however this method required too much cement and an excessively long curing time. This option was immediately ruled out for both time and cost reasons.
What were the results of the project?
Designs with an engineered geotextile were recommended after evaluating the subgrade soils along with the anticipated truck and crane loadings. An engineered geotextile having a high flow rate, good filtration, and confinement was deemed necessary due to the extremely saturated conditions of the low CBR soils. A geotextile having a high strength at a low strain was recommended for the worst conditions to help minimize the aggregate necessary for stabilizing the roads. After a successful roadway test section of 900 LF, the minimize construction delays and optimize overall costs due to the integration of the separation, reinforcement, filtration and confinement functions into a single product using Mirafi® RS380i and RS580i with 10” of aggregate.
Content is submitted by the participant. IFAI is not responsible for the content descriptions of the IAA award winners.
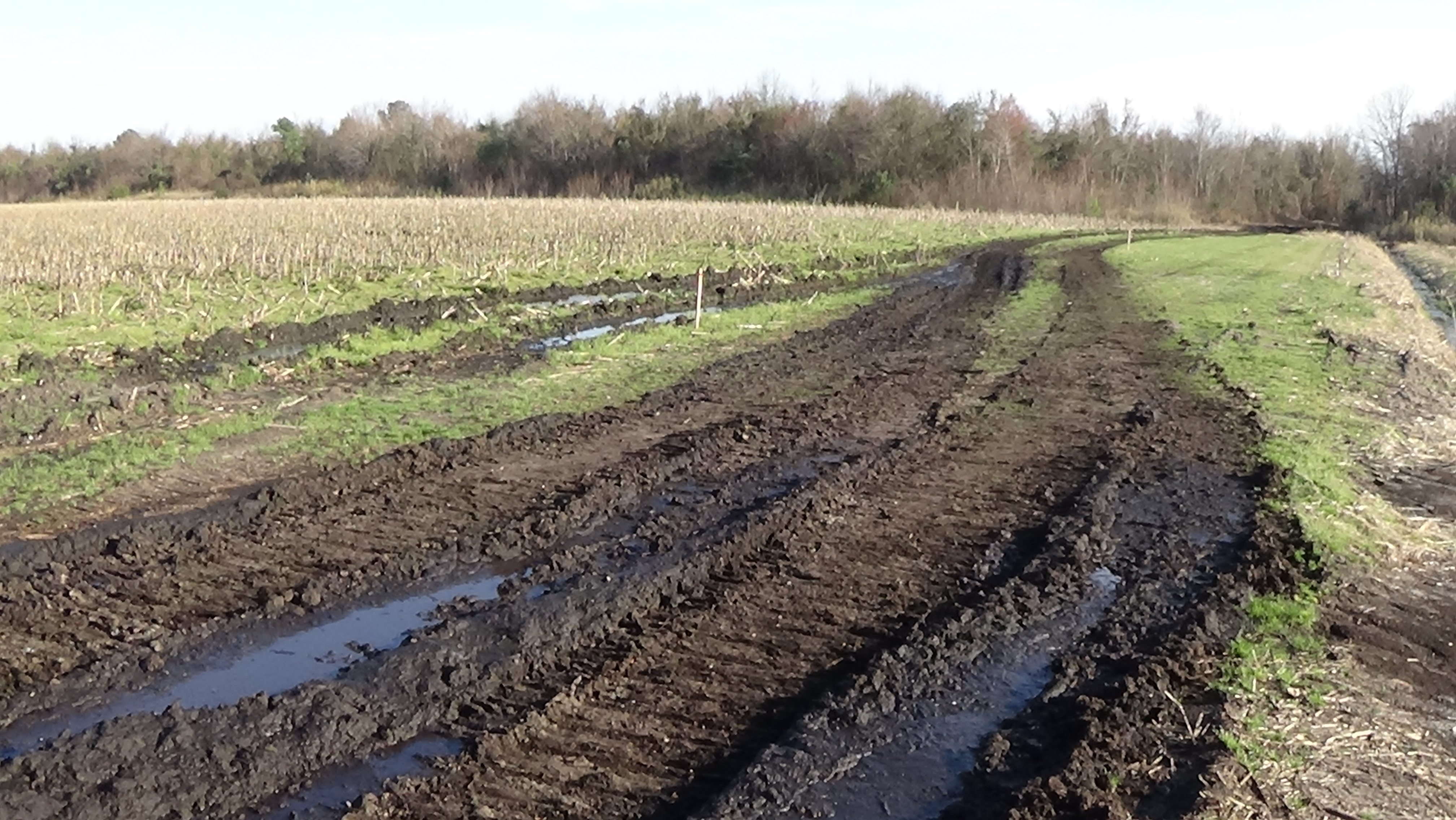
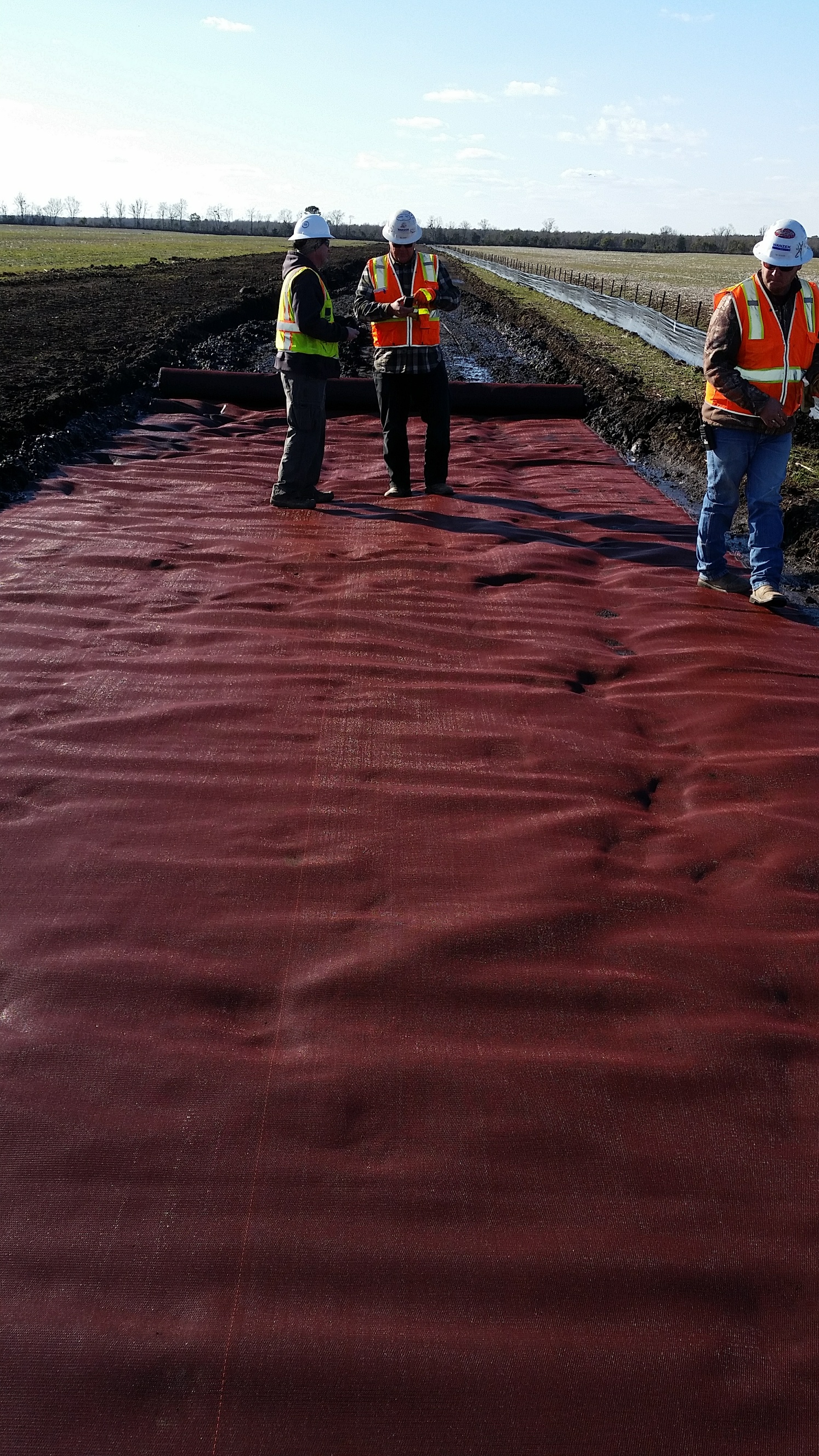
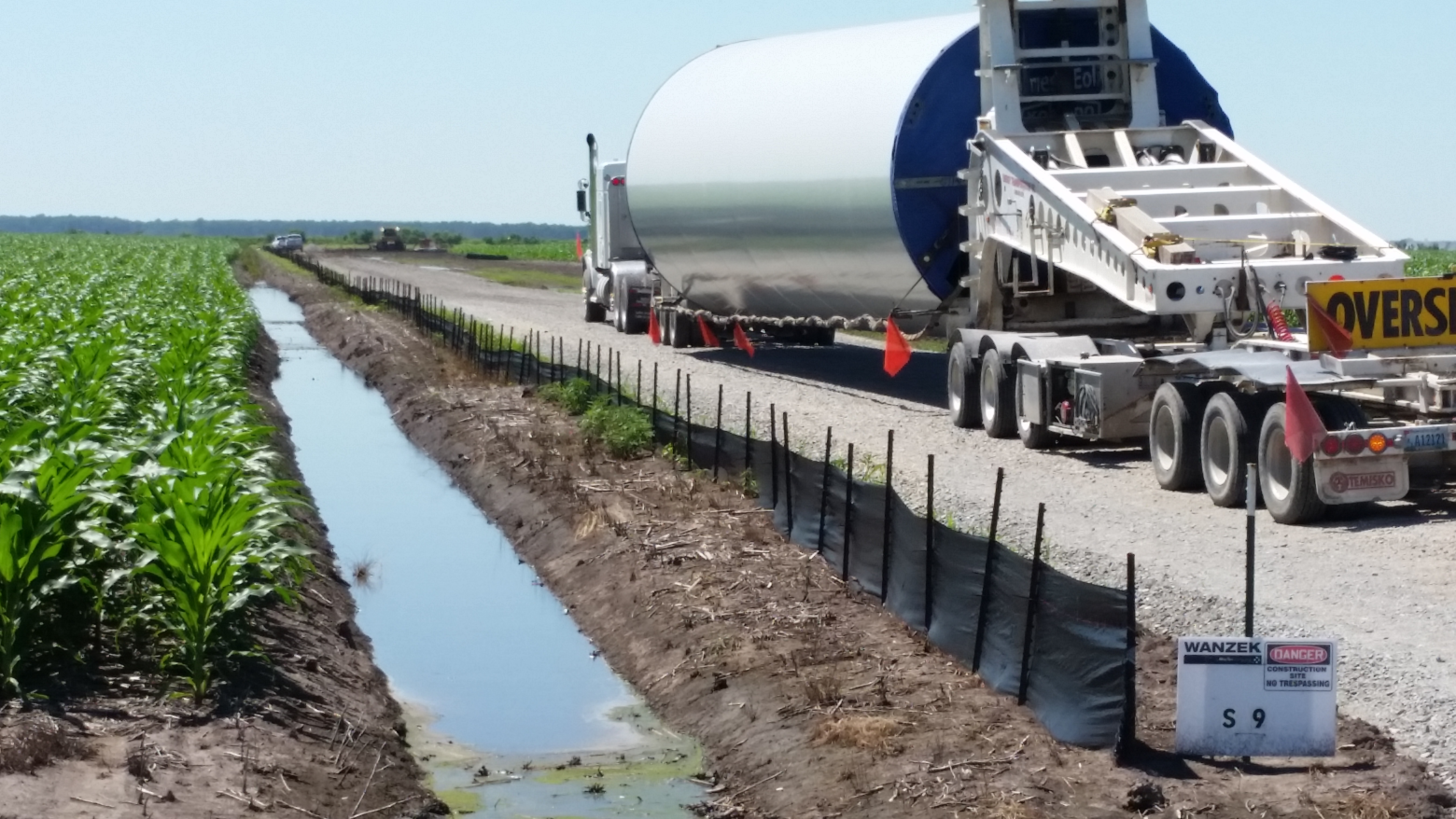
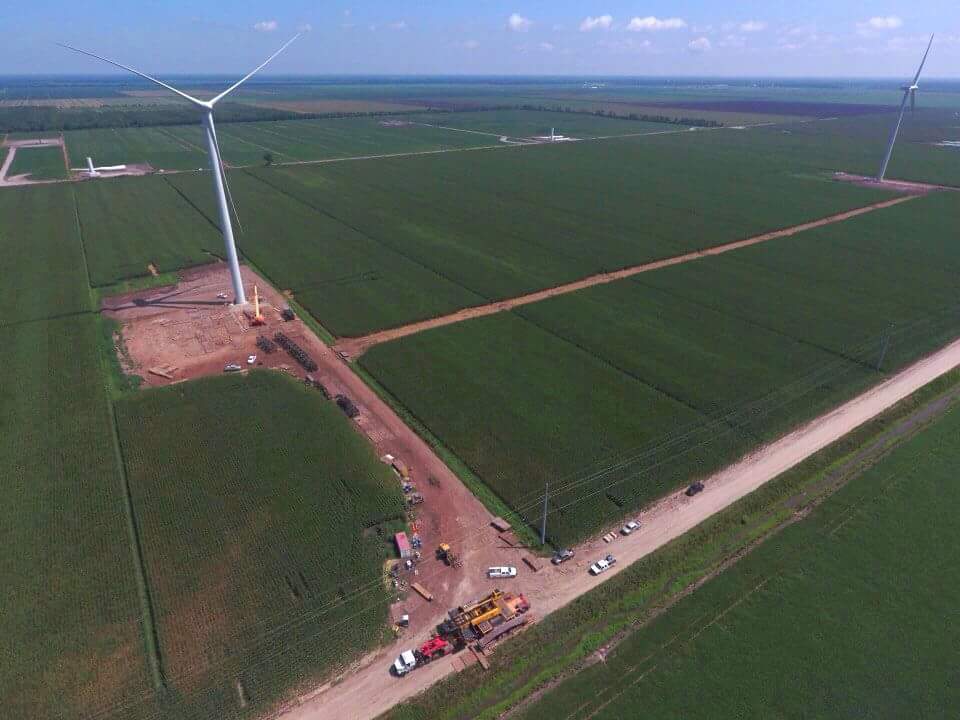